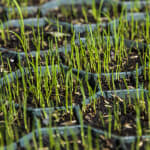
W dobie popularyzacji idei Gospodarki Obiegu Zamkniętego firmy poszukują rozwiązań, dzięki którym tworzywa sztuczne zyskują nowe zastosowania. Przykładem prowadzenia działań w zakresie gospodarki odpadami z tworzyw i wytwarzania finalnego wyrobu są ekoprodukty marki StellaGreen. O idei wykorzystania odpadów w produktach ogrodowych, ale również o tajnikach produkcji recyklatów rozmawiamy z Krystianem Duczyc, kierownikiem działu wtrysku ML Sp. z o.o.
Wasza firma jest znana przede wszystkim z wytwarzania regranulatów i wciąż niewiele osób kojarzy ML Polyolefins z marką StellaGreen.
Krystian Duczyc (kierownik działu wtrysku ML Sp. z o.o.): Rzeczywiście, mimo że działamy jako jedna spółka, funkcjonujemy pod dwiema markami, bo pomimo tego, że dział wtrysków stanowi bardzo istotny element dla fabryki regranulatów, to jednak zdecydowaliśmy się na rozdzielenie dwóch marek, które mają różne grupy docelowe odbiorców. Chociaż wiele naszych działań się uzupełnia.
Skąd wziął się pomysł na rozszerzenie działalności o wtrysk i sprzedaż gotowych produktów?
Od 20 lat zajmujemy się odpadami tworzyw sztucznych. Ilość, a przede wszystkim różnorodność tworzyw na rynku jest niesamowita, więc chcąc zaspokoić potrzeby klientów, musieliśmy zdecydować się na ich kompleksową obsługę. Specjalizujemy się w odpadach opakowaniowych, gdzie znaczną część stanowią choćby laminaty, więc musieliśmy znaleźć sposób na ich częściowe zagospodarowanie w regranulatach. Od początku było dla nas oczywiste, że będziemy mieli ograniczone możliwości testowania nowych rozwiązań u klientów, więc naturalne było dla nas zainwestowanie we własne wtryskarki. Nie chcieliśmy jednak wykorzystywać ich tylko do testów. Chcieliśmy, aby były w ciągłym użyciu, a operatorzy mieli możliwość obiektywnej oceny naszych produktów, więc musieliśmy ruszyć z produkcją. Analizowaliśmy oczywiście wiele możliwych produktów do wytwarzania, ale z racji profilu naszej działalności postawiliśmy na ekoprodukty.
Wiem, że zależało wam również na bieżącej weryfikacji wyrobów ze swojej podstawowej działalności. Czy rzeczywiście własna wtryskownia pomaga?
Jak najbardziej, to był drugi impuls, który był dla nas bardzo istotny – możliwość bieżących testów naszych produktów oraz wsparcia technicznego dla działu handlowego. Razem z moim zespołem oczekujemy tego samego co klienci, którzy szukają na rynku regranulatów wysokiej jakości. Nawiązując współpracę z nami można powiedzieć, że pierwsze testy mają już za sobą, bo przeprowadzamy je u nas. Wypuszczenie na rynek nowego tworzywa poprzedzają intensywne badania w naszej wtryskowni, a potem w firmowym laboratorium. Potem pozostaje jedynie kwestia dopasowania ostatecznej receptury do wymagań klienta.
I tu z pomocą znowu przychodzi pan, uczestnicząc w testach u klienta…
Rzeczywiście, jeżeli jest taka potrzeba, to jeżdżę z naszymi doradcami technicznymi, pomagając właściwie dobrać surowiec. Po prostu dzielę się doświadczeniem i praktyką zdobytą w czasie pracy zawodowej jako technolog. Ale nie da się ukryć, że lubię te wyjazdy również dlatego, że i dla mnie są cenną nauką. To jak seminaria z najlepszymi fachowcami w branży. Przecież pracujemy z największymi wtryskowniami w Polsce i Europie.
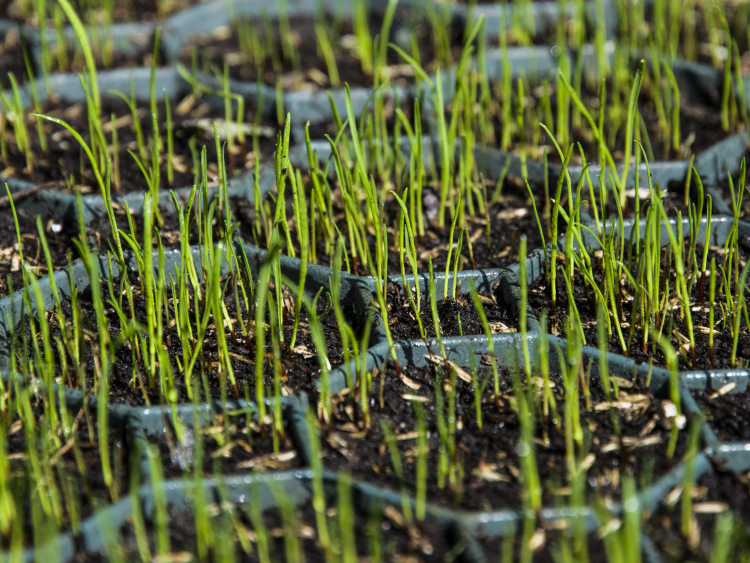
Kratka trawnikowa wykonana z recyklatu
No dobrze, ale odeszliśmy od tematu ekoproduktów – czym one tak właściwie są?
To wyroby, które powstają w wyniku ponownego zagospodarowania tworzyw sztucznych, bez wykorzystania materiałów oryginalnych. W naszym przypadku skupiamy się na małej architekturze ogrodowej, głównie kratce do stabilizacji gruntu, czy obrzeżach. Te produkty są wymagające jeśli chodzi o właściwości techniczne, ze względu na zmienne warunki atmosferyczne w czasie cyklu ich życia i stworzyliśmy dla nich odpowiednią recepturę. Dzięki naszej wiedzy i wieloletniemu doświadczeniu jesteśmy w stanie wykorzystywać odpady, które zazwyczaj trafiają na wysypisko czy do spalarni. My staramy się znaleźć dla nich nowe zastosowanie.
To jest również efekt waszej współpracy z uczelniami.
Tak, pracujemy z różnymi szkołami w Polsce i za granicą. To jest też to, co pomaga nam lepiej dopasowywać regranulaty do oczekiwań klienta. My też, sami dla siebie, opracowujemy receptury, które mają spełniać określone kryteria. Dlatego doskonale rozumiemy wymagania klientów i potrafimy się wczuć w ich potrzeby. My wiemy co sprzedajemy, bo nie tylko komponujemy nowe mieszanki tworzyw, ale też używamy ich w naszej produkcji.
Jak pan uważa jako technolog – rzeczywiście można kontrolować procesy recyklingu na tyle, aby finalne produkty były odpowiedniej jakości, powiedzmy porównywalne do oryginałów?
Najważniejsza w regranulatach jest powtarzalność. Nasze produkty nie odbiegają pod tym względem od oryginałów i mogą być ich substytutem. Widzę, że firmy generalnie mają przykre doświadczenia z regranulatami i my to zmieniamy. Na finalny efekt pożądanej jakości wpływa przede wszystkim właściwy wsad, niekoniecznie jednorodny, ale poprawnie odsegregowany, żeby móc precyzyjnie dozować poszczególne składniki mieszanki, a potem rzeczywiście proces recyklingu na odpowiednich maszynach oraz stała kontrola parametrów. Natomiast wiem z doświadczenia, że w wielu przypadkach do produkcji znakomicie sprawdzają się regranulaty, które dobrze się procesują i pozwalają zachować jej powtarzalność oraz ciągłość.
Macie ambitne plany na przyszłość, jeśli chodzi o rozwój działu wtrysków. Może pan powiedzieć coś więcej na ten temat?
Planujemy dużą inwestycję, która zdubluje nasze moce przerobowe, ale też pomoże nam zagospodarować starą część fabryki. Rozwijamy się, więc wprowadzamy nowe rozwiązania mające zwiększyć efektywność naszej pracy. Mam nadzieję, że mimo pandemii będziemy sprawnie realizować inwestycje, bo towarzyszyć im będzie również rozwój laboratorium i zakup nowych urządzeń do niego.
Rozmawiała: Agata Mojcner