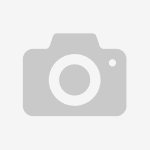
Konsekwencje wyboru nieodpowiedniego systemu gorących kanałów są poważne. Źle dobrany system gorących kanałów powoduje z reguły duże straty ciśnienia, co pociąga za sobą konieczność stosowania zbyt wysokich temperatur przetwórstwa. Następstwem tego może być np. termiczna degradacja tworzywa, smugi, przebarwienia, wady powierzchni. Będzie to wynikiem miejscowego przegrzania systemu gorących kanałów. Powoduje ono przeciążenia termiczne, które prowadzą do rozpadu surowca, tworzenia się pęcherzy lub innych negatywnych zjawisk wywołanych przez produkty rozpadu.
Wyżej wymienione tworzywa sztuczne charakteryzują się wąskim zakresem temperatur przetwórstwa pomiędzy zalecaną temperaturą wtrysku a temperaturą krzepnięcia. Konsekwencją tego jest konieczność stosowania dobrej izolacji termicznej pomiędzy systemem gorących kanałów a gniazdem formy. Dotyczy to szczególnie kanałów w rozdzielaczu oraz dysz.
Rozmieszczenie dysz musi zapewniać naturalne zrównoważenie przepływu tworzywa w rozdzielaczu. Tylko dzięki temu można uzyskać jednakowy spadek ciśnienia i jednakowy czas przebywania tworzywa w kanałach doprowadzających do każdego z gniazd. Przy wypraskach o stosunkowo małym ciężarze, z tworzyw z włóknem szklanym, zalecane jest stosowanie wtrysku pośredniego z pośrednim zimnym kanałem doprowadzającym tworzywo do kilku gniazd.
Dzięki temu większe będzie natężenie przepływu materiału przez jedną dyszę, co pozwoli na lepszą kontrolę obciążenia termicznego materiału. Można zachować odpowiednie średnice kanału doprowadzającego w gorących kanałach, równocześnie zastosować niewielką przewężkę przy każdej z wyprasek. W każdym przypadku należy przewidzieć odpowiednie miejsca naprzeciwko dysz gorących kanałów.
Dzięki temu można skierować tam zimny korek z dyszy, tak aby nie dostał się on do wypraski. Istotna jest możliwość regulacji temperatury oddzielnie dla każdej dyszy. Dlatego korzystne jest instalowanie regulatorów temperatury dla każdej ze stref.
Uzyskanie stabilnej temperatury umożliwiają np. regulatory PID. Oddzielne obiegi regulacji temperatury w bezpośrednim obszarze dysz gorących kanałów umożliwiają również optymalizację temperatury powierzchni formy. W obszarze rozdzielacza możliwe jest ugięcie płyt porównywalne z ugięciem w obszarze działania wypychaczy (brak podparcia).
Zalecane jest stosowanie rozdzielaczy o pełnym przekroju okrągłym i symetrycznie rozstawionymi elementami grzejnymi. Do tworzyw częściowo krystalicznych powinno się w miarę możliwości unikać systemów ogrzewania wewnętrznego, które mają pierścieniowy przekrój poprzeczny, ponieważ występują w nich zbyt wysokie spadki ciśnienia. Przy przetwarzaniu materiałów o małej odporności termicznej np. POM zmiana kierunku przepływu tworzywa w rozdzielaczu powinna być w miarę możliwości łagodna. W miarę możliwości należy stosować przy dyszach zewnętrzny system ogrzewania i okrągły przekrój kanału. Można wówczas uniknąć rozdzielenia masy w obszarze wlewu doprowadzającego.
Układ grzejników powinien zapewnić równomierny rozkład temperatury. Przy przetwórstwie tworzyw posiadających właściwości ścierne korzystne jest także stosowanie wymiennych końcówek. Stosuje się także układy z małą torpedą dla uzyskania dobrego oddzielenia wypraski. Przy przetwórstwie POM generalnie zaleca się stosowanie systemu z dyszami zamykanymi. Stosowane tutaj zamknięcia iglicowe pozwalają na uzyskanie małych strat ciśnienia. Istnieje bardzo wiele rozwiązań systemów gorących kanałów. Przy uwzględnieniu powyższych uwag można uzyskać bardzo dobre wyniki podczas wytwarzania różnych typów wyprasek.