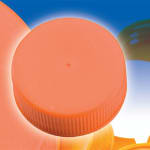
Czas cyklu ma kluczowe przełożenie na kwestie finansowe każdego przedsięwzięcia przetwórczego. Jest tak, bowiem czynnik ten bezpośrednio wpływa na koszt końcowego wyrobu, a tym samym na konkurencyjność danego producenta. I właśnie z myślą o swojej większej konkurencyjności koncern Hasco przystąpił do opracowywania technologii, która przyniosłaby znaczną redukcję czasu cyklu w formach wtryskowych.
Zdanie stworzenia 8-gniazdowej formy do produkcji nakrętek był realizowany w ramach współpracy Hasco z jednym z największym producentów opakowaniowych, amerykańską firmą Berry Plastics. W tworzeniu nowości udział brał też producent maszyn firma Arburg oraz dostawca peryferii niemiecki GWK. Wspólnie przygotowano koncepcję formy, która pomogłaby w jak największym stopniu skrócić czas cyklu.
Doprowadzono do sytuacji, w której faza wtrysku i docisku są regulowane przez precyzyjne sterowanie iglic w nowych, specjalnie zaprojektowanych do przetwórstwa poliolefin dyszach Hasco. Specjalnie dla tego projektu została wykonana również wnikliwa analiza termicznych właściwości procesu wtrysku oraz bilansu temperaturowego formy. Kalkulacje termodynamiczne oraz optymalizację procesu przeprowadzono przy zastosowaniu symulacji programowej EFD (ang. Engineering Flui Dynamics) firmy Nika z Niemiec. Optymalny czas chłodzenia został uzyskany dzięki wykorzystaniu systemów GWK.
Głównym zagadnieniem pojawiającym się przy wtrysku nakrętek jest formowanie gwintu. Zwykle w takich przypadkach stosuje się rdzenie wykręcane. Tymczasem Hasco zdecydowało się na mniej konwencjonalną metodę wyformowania za pomocą rdzeni do formowania podcięć. To wszystko pozwoliło w efekcie na skrócenie czasu cyklu o ponad 50 proc.
Oczywiste jest, że wyprodukowanie nowoczesnej formy wtryskowej na nakrętki wymaga sięgania po wiele niestandardowych symulacji. Tak było i tym razem. W efekcie jednak pierwsze próby formy przeprowadzono już po 14 tygodniach od rozpoczęcia prac.
Jednym z głównych czynników prowadzonych prac było zagadnienie chłodzenia formy. Ma ono bowiem bezpośredni wpływ na czas cyklu formy. Podczas tej fazy detal musi się schłodzić do temperatury wyformowania. Najważniejszym aspektem procesu jest rozproszenie ciepła dostarczanego wraz z tworzywem. Układ chłodzenia wkładek został zaprojektowany w ten sposób, by rozpraszanie ciepła nie było zakłócone przez ciepło doprowadzane z rozdzielacza. Aby zapewnić jak najlepszą separację termiczną we wkładkach, obiegi chłodzenia wykonano możliwie jak najbliżej gniazd według systemu „close to cavity”.