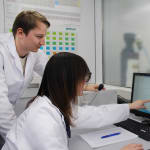
Wdrożenie innowacyjnych produktów i rozwiązań znacząco wpływa na zrównoważony rozwój w sektorze produkcyjnym. Jak przekonuje Krzysztof Wiśniewski, prezes zarządu Eurocast, dzisiaj firma przemysłowa musi opierać się na innowacyjności i dbałości o środowisko.
Eurocast to jedno z największych przedsiębiorstw przemysłowych w Polsce, które zajmuje się produkcją szerokiego asortymentu wielowarstwowych folii giętkich z polipropylenu i polietylenu oraz folii sztywnych PET. Folie są przeznaczone do produkcji opakowań do żywności oraz opakowań medycznych, a także znajdują różne zastosowania w przemyśle. W swoim parku maszynowym Eurocast dysponuje zaawansowanym technologicznie sprzętem, m.in. skaningowym kalorymetrem różnicowym, plastometrem kapilarnym, testerami przepuszczalności, mikroskopami, maszyną termoformującą, autoklawem, co umożliwia testowanie materiału opakowaniowego, jak również wykorzystywanego do procesu produkcji surowca.
Czystość i skład dostarczanych granulatów weryfikowana jest za pomocą skaningowego kalorymetru różnicowego DSC 200 F3 Maia. By uniknąć niepożądanych problemów podczas produkcji określany jest również wskaźniki płynięcia za pomocą plastometru kapilarnego LMI 5000.
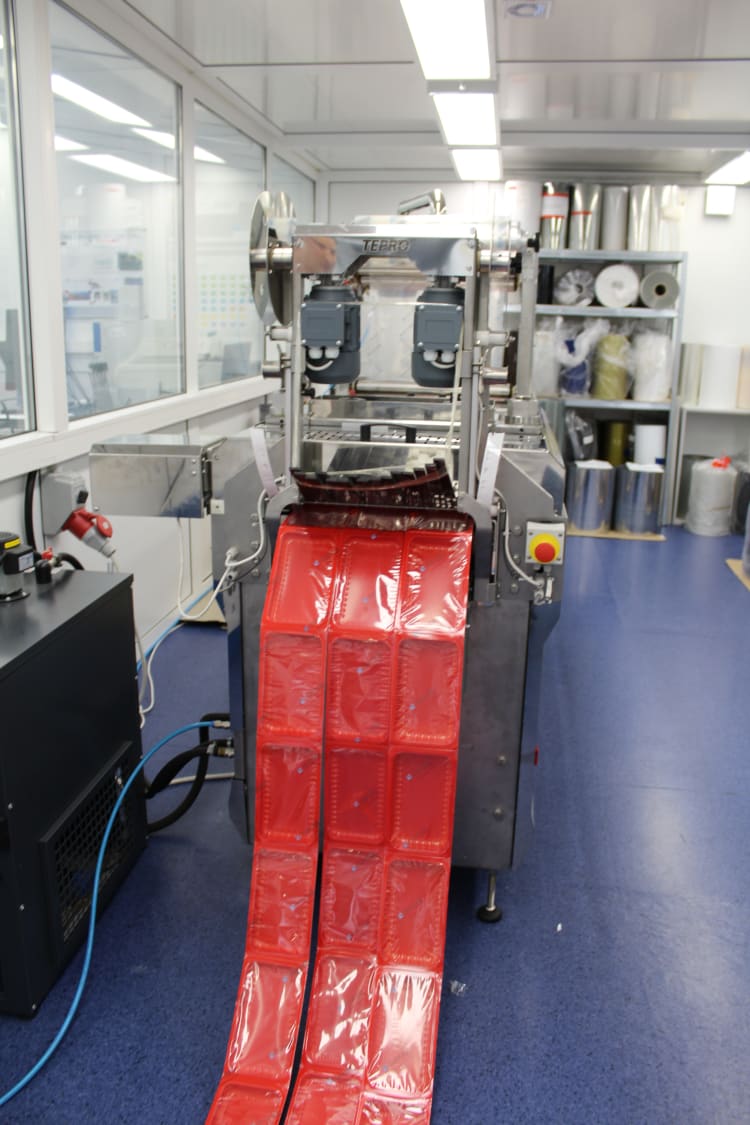
Jak mówi Krzysztof Wiśniewski, prezes zarządu Eurocast – Dzięki temu urządzeniu możemy sprawdzić czy wartości, które gwarantują nam dostawcy są zgodne z deklarowanymi. Stabilna jakość używanych surowców ma bezpośredni wpływ na jakość produkowanych asortymentów oraz ilość generowanego odpadu, który staramy się minimalizować.
Wysokiej klasy urządzenia badawcze, między innymi służące do badań przepuszczalności tlenu lub pary wodnej, wspierają pracę przedsiębiorstwa testując barierowe folie, w tym innowacyjne monofolie typu Crysta Lid. Dział Badań i Rozwoju Eurocast jest również wyposażony w dwa mikroskopy, które służą do analizy mikrostruktury, badaniu rozkładu warstw, pojedynczej warstwy wielowarstwowego materiału oraz identyfikowaniu kompozycji materiałów polimerowych. Kompaktowa linia termoformująca LPP 420 firmy TEPRO umożliwia wytworzenie całego opakowania w warunkach przemysłowych, składającego się z tacki oraz folii przykrywkowej.
- Wykorzystywana przez nas infrastruktura badawcza ułatwia wprowadzenie nowego typu materiału opakowaniowego na rynek oraz ewentualne modyfikacje struktury projektowanego wyrobu – podkreśla Damian Dziadowiec, kierownik Działu Badań i Rozwoju Eurocast. - Dzięki szeroko rozwiniętym pracom badawczym wytwarzamy nie tylko wysokiej jakości materiały opakowaniowe, które są bezpieczne w użytkowaniu, ale też nadające się do recyklingu.
Eurocast stale poszerza portfolio recyklowalnych folii. Firma do tej pory uzyskała już dwa certyfikaty wydane przez institute cyclos-http Gmbh z Aachen, potwierdzające 100% możliwość ich recyklingu, wychodząc w ten sposób na przeciw oczekiwaniom branży w aspekcie recyklingu opakowań z tworzyw sztucznych, jednocześnie spełniając wszelkie wymagania dotyczące opakowań do kontaktu z żywnością.
- W Eurocast stale inwestujemy w wysokiej klasy zaplecze technologiczne i laboratoryjne, tworząc przestrzeń do kompleksowego opracowywania nowych rozwiązań. W naszym dziale Research & Development rodzą się najbardziej innowacyjne i nieszablonowe pomysły, które w parze z realną oceną potrzeb rynku, wysoką wydajnością i jakościową produkcją pozwalają uzyskać trwałą przewagę konkurencyjną i prowadzą naszą firmę do sukcesu. Wierzymy, że innowacyjne rozwiązania realnie zmieniają oblicze branży opakowaniowej – podkreśla Krzysztof Wiśniewski.