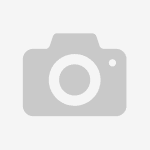
Może się zdarzyć, że otrzymamy wypraskę na powierzchni, której w okolicy wlewka widoczne będą koncentryczne pierścienie. Często mogą być tak małe, że można zauważyć tylko matową otoczkę. Czasami matowe miejsca mogą się pojawiać się również w obszarach, gdzie następują zmiany grubości ścianki.
Dlaczego powstają zmatowienia?
Do przyczyn powstawania matowych miejsc w obszarze wlewka należą przede wszystkim niewielkie rozmiary wlewka oraz co równie ważne duże prędkości wtrysku.
Podczas wtryskiwania za wlewkiem uzyskiwane są wysokie orientacje łańcuchów cząsteczkowych w wyniku dużych prędkości wtrysku, małego przekroju wlewka oraz zmiany kierunku przepływu masy plastycznej. Ponieważ bezpośrednio za nim nie ma wystarczającego czasu na relaksację, warstwy brzegowe stopu zastygają w sposób wysoko zorientowany. Zastygłe warstwy brzegowe można już tylko nieznacznie rozciągnąć i rozdzielić pod wpływem wysokich naprężeń stycznych. Przepływający wewnątrz gorący stop dopływa do ścianki formy i tworzy bardzo drobne nacięcia. Matowy efekt spowodowany jest silnie rozproszonym odbiciem na danym obszarze.
Jeżeli podczas uruchamiania wtryskarki z daną formą otrzymana zostanie wypraska z wadą powierzchniową, wówczas poprzez zmianę parametrów technologicznych można dany defekt usunąć lub go zminimalizować. Powinien to uczynić operator wtryskarki.
Protokołowanie procesu uruchamiania lub optymalizacji umożliwia kontrolę pracy osoby przeprowadzającej nastawianie oraz ocenę wpływu tego procesu na jakość wypraski. Protokół może również służyć za podstawę dyskusji, ponieważ sposób postępowania będzie bardziej zrozumiały także dla innych osób.
Protokołowanie procesu wtryskiwania należy rozpocząć w momencie wystąpienia wady technologicznej. W pierwszej części protokołu w razie potrzeby można podać ogólne dane na temat wypraski, materiału, maszyny i formy. W przypadku zmiany parametrów technologicznych pracownik może kierować się schematami działań, opisanymi w poszczególnych częściach tego cyklu. Należy jeszcze raz podkreślić, że dozwolona jest zmiana tylko jednego parametru w ciągu cyklu. Wadę można ocenić w oparciu o zaproponowane rozwiązanie dla każdej próby. Aby możliwa była również późniejsza kontrola optymalizacji, przydatne jest też oznaczenie części wykonanych w poszczególnych próbach.
Do wad powierzchniowych wyprasek należą matowe miejsca w obszarze wlewka. Ich powstawanie związane jest z niewielkimi rozmiarami wlewka, jak i dużymi prędkościami wtrysku. Poprzez zmianę odpowiednich parametrów technologicznych można ją usunąć. Pomocne w optymalizacji procesu wtrysku w przypadku wystąpienia wad powierzchniowych jest sporządzanie protokółów jego przebiegu.