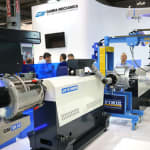
Technologia Tandem zastosowana do recyklingu tworzyw sztucznych mocno zadrukowanych i zanieczyszczonych oraz ewentualnie o wysokiej wilgotności gwarantuje doskonałą jakość granulatu przy znacznej oszczędności energii w porównaniu do konwencjonalnych systemów recyklingu, które wymagają ponownego przetłaczania materiału.
Linia składa się z zagęszczarki Compac i dwóch wytłaczarek ułożonych kaskadowo. Pierwsza, krótka wytłaczarka oraz druga wytłaczarka, ze ślimakiem o większej średnicy niż w pierwszej wytłaczarce, pozwalają na zmniejszenie szybkości ścinania („shear rate”) i mniejsze ściśnięcie przetwarzanego materiału.
Pomiędzy pierwszą i drugą wytłaczarką znajduje się wysokowydajna komora odgazowująca. W tej komorze powierzchnia materiału wystawiona na działanie podciśnienia jest 10 razy większa niż w przypadku konwencjonalnego odgazowania na cylindrze wytłaczarki, gwarantując usunięcie dużych ilości gazu i zanieczyszczeń.
Kolejną istotną cechą linii Tandem jest możliwość podwójnej filtracji. Pierwszy filtr jest montowany pomiędzy pierwszą a drugą wytłaczarką, a drugi przed granulatorem. W przypadku mocno zanieczyszczonych materiałów, pierwszy zmieniacz sit ma funkcję filtracji zgrubnej, podczas gdy drugi umożliwia dokładną filtrację materiału.