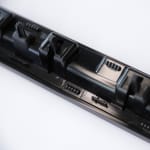
W obliczu rosnących kosztów energii oszczędność prądu jest dla wielu firm wiodącym priorytetem. Dlatego firma Rinco Ultrasonic dokonała porównania dwóch rodzajów napędu w zgrzewarkach ultradźwiękowych pod kątem ich ekonomiczności i przedstawia różnice oraz zalety obydwu napędów – nie tylko w aspekcie oszczędności energii, ale również w odniesieniu do jakości rezultatów zgrzewania.
W 2015 r. firma Rinco wprowadziła na rynek swoją pierwszą zgrzewarkę ultradźwiękową z napędem elektrycznym Electrical Motion, która uzupełniła ofertę zgrzewarek ultradźwiękowych zasilanych pneumatycznie.
W procesach zgrzewania ultradźwiękowego napęd elektryczny okazuje się bardziej energooszczędny od napędu pneumatycznego
Przemieszczanie w pionie i wywieranie nacisku podczas zgrzewania przy użyciu zgrzewarek ultradźwiękowych są zwykle realizowane za pomocą napędu pneumatycznego. Jednak w ostatnich latach coraz popularniejszy staje się napęd elektryczny.
Aby porównać urządzenia równorzędne, firma Rinco przebadała dwie maszyny o identycznej częstotliwości, mocy i skoku. Maszyny różniły się jedynie rodzajem napędu. W przypadku maszyny Electrical Motion z napędem elektrycznym uwzględniono również pracę jałową jednostki Servo Control (SCU), natomiast maszyna z napędem pneumatycznym była zasilana ciśnieniem 6 bar.
„Spodziewaliśmy się, że zgrzewarka ultradźwiękowa z napędem elektrycznym wypadnie lepiej pod względem zużycia energii, ale nie spodziewaliśmy się aż tak dużej dysproporcji”, mówi Jürgen Baumert, kierownik działu R&D w firmie Rinco Ultrasonics.
W porównaniu ze zgrzewarką zasilaną pneumatycznie maszyna Electrical Motion jest w stanie zaoszczędzić 78% energii. Przyczyn takiego stanu rzeczy należy upatrywać w samym procesie zgrzewania. Podczas pracy związanej z ruchem napęd elektryczny jest zdecydowanie wydajniejszy. Jednak napęd pneumatyczny ma przewagę podczas utrzymywania pozycji. Maszyna pneumatyczna praktycznie nie potrzebuje energii do utrzymania pozycji. Ponieważ czas utrzymywania pozycji w procesach zgrzewania ultradźwiękowego jest zazwyczaj krótszy niż sekunda, to w zasadzie nie ma to większego znaczenia. Zdecydowanie biorą górę zalety zgrzewarki ultradźwiękowej z napędem elektrycznym.
Poza tym odpada kwestia uwarunkowanych systemowo strat sprężonego powietrza z instalacji, które powodują zużycie energii również podczas przestojów. Sprężone powietrze uważa się za jedno z najdroższych źródeł energii w przemyśle.
Doskonalenie jakości efektów zgrzewania
Zgrzewarki ultradźwiękowe oferują zalety nie tylko w odniesieniu do oszczędności energii, ale również w zakresie podnoszenia jakości zgrzewania. Możliwy jest precyzyjniejszy najazd na pozycję i jej podtrzymanie. Poza tym można dowolnie programować ruch w pionie. Możliwe jest programowanie:- położenia początkowego i prędkości posuwu
- punktu hamowania i prędkości dosuwania
- samego procesu zgrzewania w 10 etapach, wybieranego jako profil siły i prędkości
- prędkości ruchu zwrotnego
Owa elastyczność w ustawianiu parametrów pozwala na jeszcze lepsze i precyzyjniej powtarzalne rezultaty zgrzewania.
Niezbitym przykładem może być nitowanie, które niedawno zostało dokładnie przebadane w centrum kompetencyjnym firmy Rinco Ultrasonics. Element górny jest wykonany z PA, element dolny z PC-ABS i zostały połączone ze sobą techniką nitowania. Operacja nitowania została przetestowana zarówno na pneumatycznej, jak i na elektrycznej zgrzewarce ultradźwiękowej. „Na obydwu maszynach udało się uzyskać odporną na obciążenie i spełniającą wymagania klienta kalotę wałeczkową”, mówi Simon Hug, szef centrum kompetencyjnego w firmie Rinco Ultrasonics. „Jednak w przypadku zgrzewarki Electrical Motion mogliśmy ustawiać parametry w sposób o wiele elastyczniejszy. Dzięki temu zwiększyła się wytrzymałość nitu i uzyskano rowek znacznie bardziej efektowny optycznie. W przypadku zgrzewarki pneumatycznej wałeczki były niedokładnie ukształtowane na skutek wycieku materiału. Ponadto na zgrzewarce Electrical Motion udało nam się niemal o połowę skrócić czas zgrzewania w porównaniu ze standardową zgrzewarką pneumatyczną, ponieważ w zgrzewarce Electrical Motion można dowolnie wybrać położenie początkowe procesu zgrzewania. W ten sposób można zaoszczędzić sporo czasu na przemieszczanie. Mając na względzie wszystkie te aspekty, klient zdecydował się na zgrzewarkę Electrical Motion”.
![]() |
![]() |
Techniki ultradźwiękowe są tak czy owak ekonomiczne
Techniki zgrzewania i cięcia przy użyciu ultradźwięków są ogólnie uważane za metody energooszczędne. Odpada kwestia podgrzewania narzędzi, jak to ma miejsce przy zgrzewaniu termicznym. Poza tym można zrezygnować z materiałów dodatkowych, takich jak śruby i kleje. Czasy taktów są krótkie, a wąska spoina umożliwia oszczędność materiału.