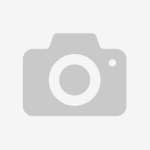
Do głównych zalet omawianej technologii należy możliwość usuwania powietrza zamkniętego pomiędzy warstwami laminatu, zagęszczenie udziału zbrojenia w laminacie zwiększające wytrzymałości, lepsza zwilżalność włókien zbrojenia i uśrednienie struktury laminatu, a także redukcja emisji szkodliwych substancji lotnych podczas utwardzania laminatu oraz izolacja powierzchni laminatu od otaczającego powietrza. T ostatnia właściwość przekłada się na lepsze dotwardzenie laminatu i eliminację kontaktu żywicy z wilgocią zawartą w powietrzu.
Prezentowana metoda umożliwia zastosowanie prawidłowo wykonanych form używanych w procesach laminowania ręcznego. Istotnym parametrem jest tutaj wielkość wyrobu i stopień jego skomplikowania. Stanowi to podstawę do projektu struktury worka próżniowego. Mimo występujących wielkich sił dociskających, konstrukcja form nie wymaga specjalnych wzmocnień, gdyż siły te są równoważone i nie powodują deformacji form. W ramach realizacji projektu dużą uwagę trzeba zwrócić na zaprojektowanie właściwej półki uszczelniającej o szerokości 10-15 cm, na której przy pomocy specjalnej taśmy uszczelnia się membranę worka próżniowego. Warto wiedzieć, że technologia produkcji kompozytów z użyciem worka próżniowego nie jest zbyt trudna.
Jak dokładnie krok po kroku wygląda produkcja kompozytów z użyciem worka próżniowego?
Zacząć należy oczywiście od systemu próżniowego. Pierwszym zadaniem, które stoi na drodze stworzenia prawidłowego systemu worka próżniowego jest konieczność wyboru pompy próżniowej o wysokiej jakości. Może to być pompa tłokowa, wirnikowa, membranowa lub inżektorowa.
Ta ostatnia pompa jest rozwiązaniem przeznaczonym głownie do tych zakładów, w których znajduje się sprężarka. Dzięki zasilaniu powietrzem pompy inżektorowe mogą być stosowane w strefach, gdzie występuje ryzyko wybuchu.
Dobór pompy jest zależny od rozmiaru formy, żądanej szybkości tworzenia próżni i ostatecznego podciśnienia. Mniejsze pompy mogą zazwyczaj uzyskiwać żądany poziom próżni również w dużych systemach jednak dużo dłużej trwa tam otrzymanie zadanego poziomu.
Jeżeli pompa nie osiąga nominalnej próżni w czasie krótszym niż 5-8 minut to prawdopodobnie jest za mała. Podstawą do doboru prawidłowej pompy jest powierzchnia formy, którą należy otoczyć workiem próżniowym. Usuwając największą możliwą ilość powietrza spod worka tuż przed jego uszczelnieniem i zastosowaniem próżni, można znacznie zredukować czas pracy pompy. Warto tez zdawać sobie sprawę, że w ramach budowy systemu próżniowego zaleca się stosowanie manometru lub manometru z regulatorem. Niekiedy jest to nawet niezbędne. Jest tak gdyż manometr pozwala na wizualne wykrywanie nieszczelności. Dodatkowo dokładnie pokazuje narastające podciśnienie podczas operacji, które można dokumentować.
Rejestracja danych przemijającego czasu w każdym poziomie próżni pomaga dokładnie powtarzać proces produkcji. Zastosowanie próżni przy produkcji laminatów poliestrowych wymaga bezwzględnie wykorzystania manometru ze względu na nieprzekraczalne wartości podciśnienia. Najkorzystniejszym pomiarem podciśnienia próżni jest pomiar przez manometr, wskazujący podciśnienie wewnątrz worka. Jest to szczególnie pomocne w sytuacji gdy worki pracują na zmiennych poziomach próżni.