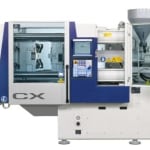
Formowanie wtryskowe w warunkach czystych pomieszczeń odbywa się przeważnie w „pomieszczeniach czystych” tzw. clean rooms i „pomieszczeniach nieskazitelnie czystych”. Oprócz danych przekazywanych przez odbiorcę dla klasyfikacji decydujący jest cel zastosowania wytwarzanych artykułów. Zasadniczo dokonuje się rozróżnienia pomiędzy technicznymi i farmaceutycznymi pomieszczeniami czystymi. Dla zastosowań technicznych wymagane jest z reguły otoczenie pozbawione pyłu, podczas gdy dla zastosowań farmaceutycznych i medycznych decydujący jest także brak zarazków w otoczeniu, a tym samym w produkowanych artykułach. Ogólnie jednak w technice pomieszczeń czystych mówi się przede wszystkim o „braku cząsteczek”, gdyż także mgła olejowa może przykładowo powodować niepożądane skażenie.
Dalszym mankamentem przy pracy wtryskarek w pomieszczeniach czystych jest ich „duża ilość ruchów” uwarunkowana sposobem pracy. Konkretnie: ruchy otwierania i zamykania maszyny powodują zawirowania powietrza, które z kolei uwalniają pyły i inne cząsteczki w niekontrolowanych ilościach.
Ruchome elementy konstrukcyjne są z reguły smarowane (płozy ślizgowe, prowadnice, tuleje kolumn w płytach ruchomych, układy regulacji wysokości form) i zwilżają mijane nieruchome części wtryskarek mniej lub bardziej grubą warstewką smaru. Uwalniane są przy tym lotne cząsteczki (kropelki oleju). Ten strumień cząsteczek zwiększa się wraz ze wzrostem temperatury maszyny i środka smarnego. Najbardziej niekorzystna jest warstewka smaru przyczepiająca się do kolumn i prowadnic szynowych płyt ruchomych i znajdująca się przez to w bezpośrednim sąsiedztwie wytwarzanych produktów. Napędy lub cylindry hydrauliczne należy ocenić w podobny sposób. Podwyższone ryzyko skażenia wynika przy tym z obecności uszczelek. Wysokie ciśnienia hydrauliczne, nawet w przypadku nieuszkodzonych maszyn, prowadzą do wytwarzania przez uszczelki drobnych rozprysków oleju niewidocznych gołym okiem.
Aby sprostać wymaganiom należy przy wyposażaniu maszyn zwracać szczególną uwagę na to, że profilaktyczne utrzymywanie maszyn w dobrym stanie zaczyna się już przy zamawianiu maszyn. Oto niektóre podstawowe wymagania odnośnie wykonania urządzeń produkcyjnych przeznaczonych do pracy w pomieszczeniach czystych:
- Antystatyczna powłoka lakiernicza – dla uniknięcia naładowań i rozładowań elektrostatycznych przyciągających zanieczyszczenia. Generalnie powierzchnie powinny być wolne od porów, gładkie i bez rys lub otworów. Materiały powierzchniowe muszą być odporne na działanie środków czyszczących i dezynfekujących.
- Konstrukcja korzystna z punktu widzenia przepływów – szczególnie wewnętrzne obszary urządzeń i maszyn muszą być gładkie, pozbawione występów i uskoków, nie mogą posiadać martwych naroży ale powinny mieć naroża zaokrąglone oraz czyste przejścia.
- Stosowane mogą być wyłącznie dozwolone materiały eksploatacyjne, takie jak oleje smarne i olej hydrauliczne.
- Przewody mediów i czynników energetycznych muszą być tak hermetyczne, aby ich zużycie ścierne było wyeliminowane w największym możliwym stopniu.
- Jednostka zamykania zoptymalizowana dla konkretnego przypadku zastosowania.
- Wystarczająca filtracja pozwalająca na uzyskiwanie klas czystości 15/12/09 i lepszych. Jeśli jest to możliwe wartość tę należy uzyskiwać przy pomocy filtra w układzie. Instalowane dodatkowo filtry w odgałęzieniach posiadają dodatkowe elementy konstrukcyjne podwyższające ryzyko skażenia.
- Wymóg dostarczania przez producenta maszyn po przepłukaniu z zapewnieniem klasy czystości 16/13/10 lub lepszej.