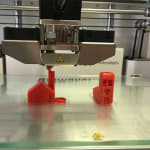
Manuel Delgado, Market Manager działu Druku 3D w Velox, przedstawia kilka nowych surowców specjalnych przygotowanych z myślą o produkcji filamentów i proszków. Przejście do produkcji elementów funkcyjnych w dużym stopniu zależy od doboru odpowiednich surowców, które spełniają nie tylko wymóg dokładności konstrukcyjnej, lecz również zapewniają aplikacji odpowiednie właściwości fizyczne oraz mechaniczne. Wymagania stawiane przed elementami i komponentami wykonanymi w technologii druku 3D mogą kształtować się diametralnie różnie w zależności od danej branży, dlatego też integracja tej technologii w proces produkcyjny znajduje się na różnych etapach. W niektórych branżach, np. przemyśle lotniczym i kosmonautyce lub branży automotive, drukowanie przestrzenne jest już na porządku dziennym. W innych gałęziach przemysłu, np. w branży medycznej, spożywczej i opakowaniowej, wytwarzanie produktów dla konsumentów z wykorzystaniem druku 3D znajduje się jeszcze w powijakach.
Z jednej strony powodów takiego stanu rzeczy należy doszukiwać się w rozbudowanych przepisach i normach, które regulują możliwości stosowania elementów wytworzonych za pomocą druku 3D, mocno je ograniczając lub całkowicie wykluczając. Zastosowanie znajdują różne regulacje w zależności od tego, czy chodzi o element maszyny taki jak np. koło zębate - inne wymagania będą obowiązywały w przypadku wymyślnych pojemników na żywność. I tak w Europie materiały, które są przeznaczone do bezpośredniego kontaktu z żywnością, muszą uzyskać certyfikację zgodną z Rozporządzeniem Komisji (WE) nr 10/2011 z dnia 14 stycznia 2011 r. Aby mogły być rozprowadzane na globalną skalę muszą ponadto być zgodne z normą FDA.
Z drugiej strony materiały te muszą spełniać praktyczne wymaganiom procesów, w których będą wykorzystywane. Nie dotyczy to tylko trwałości i twardości, lecz tyczy się to także innych czynników, takich jak np. jakość powierzchni. Od dodatków i filamentów wykorzystywanych w branży spożywczej oraz medycznej wymaga się czystości graniczącej ze sterylnością. Wiele elementów tworzonych przy pomocy technologii druku 3D posiada trudne do czyszczenia, porowate powierzchnie, co stanowi spore utrudnienie w przypadku łączenia warstw. O ile takie elementy można jeszcze zaakceptować w charakterze dowodu poprawności projektu (ang. Proof of Concept), nie nadają się one do praktycznego stosowania w przypadku czyszczenia chemicznego i/lub parowego. Rozwiązaniem tego problemu są specjalne surowce i dodatki, tworzone z myślą o takich właśnie zastosowaniach.
W metodzie FDM (osadzanie topionego materiału, ang. fused deposition modelling), nazywanej również FFF (ang. fused filament fabrication) najczęściej stosuje się kopolimer akrylonitrylo-butadieno-styrenowy (ABS) i polilaktyd (poli kwas mlekowy, PLA). Oba wymienione materiały to tworzywa termoplastyczne, które po podgrzaniu do odpowiedniej temperatury można dowolnie formować. Tworzywo ABS powstaje z ropy naftowej i najczęściej wykorzystywane jest do produkcji wytrzymałych elementów, wykorzystywanych np. w branży automotive. Niska temperatura topnienia sprawia, że praca z tym tworzywem jest stosunkowo łatwa i bezpieczna, przekłada się to jednak również na podatność tak wydrukowanych elementów na deformacje, rysy i topnienie.
Nawet jeśli ABS i PLA należą do tworzyw sztucznych, które są najczęściej wykorzystywane do druku 3D, standardowe typy tych tworzyw z ww. powodów nie nadają się do użycia w bardziej ambitnych lub silnie regulowanych gałęziach przemysłu. Jednakże w zależności od danego obszaru zastosowania wyspecjalizowane warianty materiałów ABS lub PLA mogą zapewnić sukces. Istnieją takie warianty materiału ABS, jak np. Magnum ABS produkowane przez Trinseo, który spełnia normę ISO 10993 w związku z czym jest sklasyfikowany jako materiał biozgodny, dzięki czemu jest dopuszczony do zastosowań medycznych. Wspomniany materiał w odróżnieniu od standardowych wariantów ABS charakteryzuje się ponadto lepszą odpornością na uderzenia, jak i wysokiej jakości, połyskliwym wyglądem, co czyni go użytecznym dla branży medycznej. Inne typy materiału ABS oferują takie właściwości jak: wysoka odporność termiczna, bezhalogenowa niepalność, odporność na korozyjne otoczenie umożliwiająca czyszczenie chemiczne bądź parowe. Podobne modyfikacje mogą sprawić, że wyspecjalizowane materiały PLA będą odpowiednie do przemysłowych zastosowań. SK Chemicals w serii Skyplete rozwija warianty PLA, które po rozżarzeniu osiągają operacyjną odporność termiczną nawet do 100 °C.