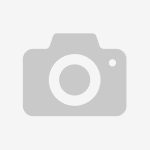
Węglowodory poddane działaniu wysokich temperatur ulegają rozkładowi. Procesy termicznego rozkładu węglowodorów z wytworzeniem produktów węglowodorowych o mniejszej masie cząsteczkowej w porównaniu z masą cząsteczkową stosowanego surowca nazywa się krakowaniem.
W procesie krakowania katalitycznego używa się najczęściej mazut lub frakcje olejowe otrzymane podczas jego destylacji próżniowej. Stosować można również wszystkie inne frakcje ropy naftowej o wyższych temperaturach wrzenia. W warunkach przemysłowych najczęściej poddaje się rozkładowi surowiec o charakterze parafinowym i ciężkim składzie frakcyjnym. Przemysłowe procesy krakowania katalitycznego prowadzone są w fazie gazowej, w obecności stałych katalizatorów heterogenicznych. Przebiegają w temperaturze ok. 450 st. C, pod ciśnieniem zbliżonym do atmosferycznego. Katalizatorami krakowania katalitycznego są syntetyczne glinokrzemiany otrzymane w reakcji soli glinu z hydrożelem krzemionkowym.
Kraking katalityczny jest też coraz powszechniej wykorzystywany do chemicznego recyklingu tworzyw sztucznych, zwłaszcza polipropylenu, polietylenu oraz polistyrenu z recyklingu.
Tworzywa sztuczne stanowią około 10 proc. odpadów stałych. Wśród nich wyróżniamy w 80 proc. poliolefiny, czyli polipropylen i polietylen, w 12 proc. polistyren, a w 5 proc. polichlorek winylu. W wyniku krakingu katalitycznego odpady mogą być przetwarzane na wartościowe komponenty dla przemysłu petrochemicznego i rafinerii, a nawet na monomery dla wtórnego wytworzenia polimerów.
Kraking prowadzony jest bez dostępu powietrza i w zakresie temperatur 350-500 st. C. Jedną z technologii jest proces oparty na reaktorze pracującym ze złożem fluidalnym, gdzie fazą fluidalną jest rozdrobniona krzemionka zawieszona w produkcie gazowym.
Produkty takiego krakingu to w 8 proc. gazy C1-C4, w 21 proc. frakcja o temperaturze wrzenia poniżej 180 st. C, w 54 proc. frakcje o temperaturze wrzenia w zakresie 180-365 st. C, i w 17 proc. gacz parafinowy wrzący powyżej 365 st. C.
Technologia ta według projektu koncernu BASF polega na dwustopniowym procesie, w którym w pierwszym etapie w temperaturze 300-350 st. C następuje upłynnienie tworzywa. Polega to na tym, że po spłynięciu do właściwego krakera tworzywo sztuczne ulega rozkładowi w temperaturze 400-450 st. C. Głównym produktem procesu jest ciekła frakcja odpowiadająca zakresowi wrzenia benzyny i oleju napędowego.
Instalacja do prowadzenia krakingu składa się z reaktora o pojemności 6 m3 wykonanego ze stali, posadowionego na piecu z palnikami i zaopatrzonego w śluzę umożliwiającą ciągłe dozowanie surowca w ilości 30-50 kg wraz z odpowiednio dobranym katalizatorem. Katalizator ten stanowi mieszaninę związków glinu i innych metali. Ponadto instalacja jest wyposażona w kolumnę rektyfikacyją wypełnioną pierścieniami i zaopatrzoną w dwa skraplacze, pozwalającą na zbieranie dwu frakcji ciekłych oraz gazów i zespołu termopar, (pozwalających mierzyć temperatury wewnątrz reaktora i na szczycie kolumny) oraz w warstwę metalu o temperaturze topnienia ok. 80 st. C służącą jako wymiennik ciepła.