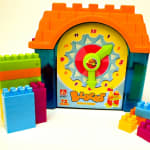
Formowanie rotacyjne sprawdza się zarówno dla odbiorców przemysłowych, jak i indywidualnych. Jeśli bowiem potrzebne są wydrążone części o szczególnie skomplikowanych i różnorodnych kształtach, wówczas rozwiązaniem mogą być tworzywa formowane rotacyjnie. Dzięki temu wyjątkowemu, szybko rozwijającemu się procesowi technologicznemu, możliwe jest dostosowanie projektu i materiałów do specyficznych wymagań odbiorcy. Technologia formowania rotacyjnego przewyższa zatem inne technologie formowania pod takimi względami jak redukcja kosztów, ekonomiczne serie produkcyjne i wymiary części. Ponadto produkty formowania rotacyjnego często stanowią lżejszy zamiennik tradycyjnie stosowanych materiałów.
Usprawniona technologia formowania rotacyjnego przyczyniła się już do postępów w sterowaniu procesem technologicznym oraz podniesienia jakości żywic odlewniczych i konstrukcji formy. Dzięki skomputeryzowanemu sprzętowi i coraz większemu wyborowi żywic i składników, metoda ta pozwala gwałtownie zwiększyć zakres produkcji: od produktów o bardziej tradycyjnych rozmiarach, takich jak choćby strzykawki z plastizolu do płukania uszu aż do ogromnych naczyń polietylenowych o pojemności ponad 80 tys. litrów.
Po wprowadzeniu zasypanej formy do pieca, obraca się ona w dwóch osiach. W miarę jak ciepło przenika do formy, żywica osadza się na wewnętrznej powierzchni formy aż do pełnego zlania. Wówczas forma jest chłodzona powietrzem lub rozpyloną wodą, albo nawet poprzez połączenie obydwu tych sposobów. Forma cały czas obraca się, a temperatura jest obniżana stopniowo. Następnie jest otwierana, a wykonana część zostaje usunięta. W tym samym czasie forma jest kierowana do następnego cyklu produkcji.