Wymienione środki pomocnicze dzieli się na kilka kategorii, w tym smary wewnętrzne/dyspergatory, smary zewnętrzne i peptyzatory. Dyspergatory ułatwiają poślizg między makrocząsteczkami kauczuku, skutecznie zwilżają powierzchnię napełniaczy, a tym samym poprawiają ich dyspersję w matrycy polimerowej.
Smary zewnętrzne charakteryzują się niską mieszalnością z kauczukiem i mają tendencję do migracji na powierzchnię mieszanek, ułatwiając tym samym późniejsze operacje przetwórcze - wytłaczania czy wtrysku - poprzez zmniejszenie oporów przepływu w urządzeniach produkcyjnych. Peptyzatory są zaś akceptorami wolnych rodników lub katalizatorami utleniania, które skutecznie usuwają wolne rodniki powstające w trakcie wykonywania mieszanki kauczukowej. Hamują rekombinację makrorodników i ułatwiają uplastycznianie kauczuku.
Znaczne ilości środków pomocniczych stosuje się w przemyśle oponowym. Wśród producentów artykułów technicznych podejście do wykorzystania tego typu substancji jest zróżnicowane. Niektórzy stosują je jako standard, inni jako dodatek do niektórych typów mieszanek (w zależności od używanych urządzeń), jeszcze inni uważają, że nie mają one żadnego wpływu. Z całą pewnością, ze względu na różnorodność dostępnych na rynku produktów i ich złożony skład, dokonanie właściwego wyboru jest trudne. Dlatego też warto zadbać o jakość stosowanych surowców i ich zgodność ze specyfikacjami, aby ograniczyć produkcję mieszanek niespełniających wymagań.
Aby skrócić czas sporządzania mieszanek w wytwórniach, bele kauczuku kondycjonuje się (podgrzewa) przed operacją mieszania. Tradycyjna metoda polega na wykorzystaniu pomieszczenia magazynowego ogrzanego do 80°C, w którym materiał jest przechowywany przez kilka dni. Duże oszczędności w poborze energii można uzyskać, jeśli zadba się o właściwą kubaturę takiego pomieszczenia oraz zapewni się odpowiednią izolację jego ścian i stropu. Kolejnym krokiem w kierunku energooszczędności będzie rozmieszczenie surowców w sposób ułatwiający ich ogrzewanie i umożliwiający właściwą cyrkulację powietrza. Dodatkowo, użycie wentylatorów pozwoli zniwelować zjawisko stratyfikacji ciepła w pomieszczeniu (ciepłe powietrze rozwarstwia się w każdym pomieszczeniu, co może powodować znaczne różnice temperatur między podłogą a sufitem, nawet do 15°C).
Oczywiście można zastosować do podgrzewania kauczuków i mieszanek urządzenia mikrofalowe, jednak w tym przypadku koszty inwestycyjne są znaczne. Dla niedużych, średnich i małych przedsiębiorstw opisane wyżej, proste czynności wydają się bardziej racjonalne. Jeśli producent wyrobów gumowych kupuje niewielkie ilości mieszanek, wystarczy że przed przystąpieniem do konfekcjonowania podgrzeje je i odświeży na walcach.
Wytwórcy mogą poszukiwać oszczędności w optymalizacji pracy chłodnic festonowych wykorzystywanych do chłodzenia wyprodukowanych mieszanek kauczukowych. Bardziej efektywne będą urządzenia wykorzystujące przeciwprądowe przepływy powietrza (w kierunku przeciwnym do zasilania mieszanką), ale większe oszczędności można uzyskać wyłączając wentylatory w momencie, gdy cały arkusz gumy jest już schłodzony. Teoretycznie jednostkowe zużycie energii podczas formowania gumy wynosi 0,1 kWh/kg, ale rzeczywiste wyniki wahają się od 0,3 kWh/kg do 2 kWh/kg, co daje sprawność na poziomie 33% i 5%. Większość wydatkowanej energii jest tracona do ogrzania maszyn, form i otoczenia.
Straty ciepła są głównym źródłem niskiej efektywności, ale można je zmniejszyć, właściwie izolując elementy urządzeń formujących. Z pewnością szybko da się zauważyć niższe zapotrzebowanie na energię elektryczną czy parę. Ponadto poprawi się komfort pracy i bezpieczeństwo operatorów maszyn.
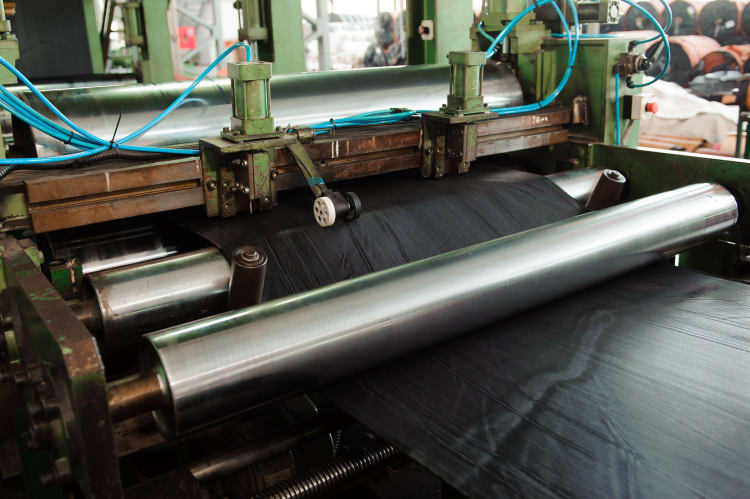
Oszczędności przyniesie również optymalizacja procesu wulkanizacji - parametrów takich jak temperatura, czas i ciśnienie. Guma słabo przewodzi ciepło i zwiększanie temperatury nie jest technologicznie uzasadnione. Wyrób w takim przypadku może być przewulkanizowany od zewnątrz, podczas gdy w środku proces sieciowania nie zajdzie w wystarczającym stopniu. Tego typu zjawisko można zaobserwować zwłaszcza w przypadku wyrobów grubościennych i wielkogabarytowych. Przy wyznaczaniu optymalnego czasu wulkanizacji warto posłużyć się wykresem z reometru lub skorzystać z informacji o optymalnym czasie wulkanizacji podanych przez producenta. Zbyt duży nacisk na formę wulkanizacyjną może doprowadzić do jej uszkodzenia lub przedwczesnego zużycia.
Optymalizacja procesu wulkanizacji zapewnia nie tylko mniejsze straty energii, ale również lepszą jakość wytwarzanych wyrobów i mniejszą ilość odpadów. Poprawia się ekonomika produkcji. Oprócz izolacji urządzeń ogrzewanych elektrycznie, warto przeprowadzić modernizację układów kontrolujących temperaturę.
Urządzenia do wulkanizacji nagrzewają się dość długo, dlatego warto wyposażyć je w zegary umożliwiające wcześniejsze, automatyczne załączenie tak, aby były gotowe do pracy przed rozpoczęciem zmiany. Pozytywne efekty przyniesie także kontrola i zapewnienie właściwych nastaw w czasie pracy, bowiem operatorzy mogą „podkręcać” ustawienia. Zwiększy się w ten sposób produktywność, zwłaszcza w małych zakładach wytwórczych.