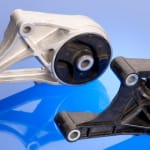
Nowy komponent służy do zabezpieczenia silnika pojazdu i zespołu transmisyjnego oraz do tłumienia drgań i zmniejszenia hałasu powodowanego przez konstrukcję pojazdu. Do tej pory wysoko obciążone komponenty - zawieszenie silnika, zawieszenie przekładni i drążki reakcyjne - wykonywano wyłącznie z aluminium lub stali. Teraz jednak sięgnięto po tworzywo sztuczne. Wybór padł na poliamid o nazwie Ultramid A3WG10 CR.
Nowo stworzona część waży o 35 proc. mniej niż jej aluminiowe poprzedniczki i weszła do produkcji seryjnej dla modeli Opel Vectra i Saab. System zawieszenia silnika stanowi element podstawowego połączenia między zespołem silnika i układu transmisyjnego a nadwoziem. Oprócz dużych obciążeń systemy te wystawione są na temperatury od - 30 st. C do 120 st. C oraz na zanieczyszczenie olejami i różnymi chemikaliami.
System zawieszenia silnika ze specjalnego tworzywa to odpowiedź na aktualne wyzwania przemysłu. Chociaż producenci samochodów nieustannie zmierzają ku coraz lżejszym konstrukcjom, to jednak nadal używali stali i aluminium do elementów konstrukcyjnych pojazdu narażonych na obciążenia – w tym także do systemów zawieszenia silnika.
Czym cechuje się tworzywo BASF?
W rodzinie materiałów Ultramid CR zależność właściwości materiału od orientacji włókna i szybkości odkształcenia zostały ustalone precyzyjnie. Poziom osiągów tych tworzyw jest wyższy, a odchylenie standardowe własności mechanicznych mniejsze niż u poliamidów dostępnych na rynku. Źródła zaopatrzenia zostały starannie wyselekcjonowane, a warunki produkcji podlegają ścisłej kontroli, tak aby komponenty wykonane z tych tworzyw utrzymywały stały poziom jakości i wyliczone właściwości dokładnie odpowiadały doświadczeniom.
Najważniejsza część innowacji dostarczonej przez wykorzystanie tworzywa BASF, czyli wszechstronne obliczenia i symulacja, opierała się na instrumencie BASF do symulacji integracyjnej.
W celu uzyskania niezawodności przewidywań wytrzymałości bardzo obciążonego zawieszenia silnika, BASF rozszerzył możliwości tego narzędzia. W metodzie wymiarowania części, aktualnie szeroko używanej w przemyśle, obliczenia dokonuje się niezależnie od procesu symulacji, który posługuje się tylko średnimi wartościami właściwości charakterystycznych materiału.
W celu lepszego wykorzystania możliwości poliamidów wzmocnionych włóknem trzeba jednak wziąć pod uwagę orientację włókna w różnych miejscach części, ponieważ właściwości mechaniczne zmieniają się dość znacznie w zależności od ułożenia włókna. I właśnie tutaj wkracza symulacja integracyjna: łączy ona wyniki symulacji wypełniania z analizą elementu skończonego, w której bierze się pod uwagę orientację włókna w całej analizowanej części. Te wyniki oraz wpływ temperatury i współczynnik obciążenia posłużą do wymiarowania komponentu i formy. Kompleksowy test cyklu życia oraz ostateczne testy pojazdu Opel wykazały, że symulacja integracyjna pozwala na wykonanie bardzo wiarygodnego projektu komponentu.