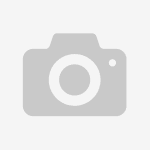
Można ogólnie stwierdzić, że jakość wykonania komponentów układów hydraulicznych oraz maszyn w ostatnich latach uległa znaczącej poprawie. Już dawno zauważono, że przy optymalnej czystości oleju maszyny pracują z mniejszą ilością zakłóceń, a ich trwałość może ulec znacznemu wydłużeniu. Dla uniknięcia zużycia konieczny jest zatem wymóg absolutnie czystej cieczy roboczej. Jest to technicznie możliwe, ale wiąże się ze zbyt wysokimi kosztami.
Faza 1 - klasy czystości od 22/19/16 do 20/17/14
Dokładność filtracji wynosi od 10 do 12μm, przy równoczesnym niskim stopniu separacji na filtrze i niewielkiej wydajności cyrkulacji filtrowanego oleju przez jednostkę zbiornikową. Pielęgnacja oleju nie jest przeprowadzana. Występują wysokie koszty awarii komponentów układu hydraulicznego.
Faza 2 - klasy czystości od 19/16/13 do 18/15/12
Filtry o dokładności od 10 do 12μm mają większy stopień separacji, a wydajność cyrkulacji przez zbiornik została podwyższona. Nie jest przeprowadzana dodatkowa pielęgnacja oleju. Dyspozycyjność urządzeń wzrasta.
Faza 3 - klasy czystości od 17/14/10 do 13/10/07
Dokładność filtracji od 5 do 12 μm z dużym stopniem separacji, wysoka wydajność cyrkulacji przez zbiornik i dodatkowa filtracja obejściowa o dokładności od 1 do 3 μm. Filtracja ciśnieniowa o dokładności 3 μm i wysokim stopniu cyrkulacji. Filtr umieszczony w odgałęzieniu z 4- do 5-krotną cyrkulacją przez zbiornik na godzinę i dokładnością od 1 do 3 μm. Realizowana jest dodatkowa pielęgnacja oleju, jakość oleju jest mierzona i kontrolowana. Należy przy tym podkreślić, że przy wysokiej dokładności filtracji (1 do 3 μm) koszty pielęgnacji początkowo wzrastają w wyniku czyszczenia zbiornika. Jednak po oczyszczeniu jednostki zbiornikowej ponownie spadają. Dyspozycyjność urządzenia jest optymalna.
Faza 4 - duże nakłady na pielęgnację oleju
Przy dużych kosztach pielęgnacji oleju klasa czystości ulega tylko minimalnej dalszej poprawie. Dyspozycyjność urządzeń również wzrasta tylko nieznacznie.
Wysokie koszty powstają przy tym z następujących przyczyn:
- koszty zakupów i rosnące zużycie energii wskutek zbyt rozbudowanej koncepcji filtracji,
- duże nakłady na obsługę wskutek zastosowanych dodatkowo filtrów bez ich automatycznej kontroli przez układ sterowania maszyny,
- drogie urządzenia dodatkowe do pielęgnacji oleju, które muszą być kontrolowane i przełączane przez personel z maszyny na maszynę,
- za małe filtry o wysokich początkowych różnicach ciśnienia i krótkiej trwałości.
Konieczne staje się zdefiniowanie klasy czystości możliwej do technicznego zrealizowania, gwarantującej optymalne zabezpieczenie przed zużyciem, a równocześnie możliwej do utrzymania w praktyce przy dających się zaaprobować nakładach.