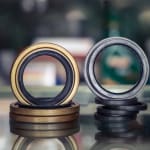
Artykuły gumowo-metalowe są powszechnie wykorzystywane w rozmaitych zastosowaniach przemysłowych. Aby optymalnie spełniały swoją rolę, muszą być projektowane z zachowaniem dbałości o szczegóły - przekłada się to bowiem bezpośrednio na ich końcową trwałość i wytrzymałość.
Techniczne wyroby gumowo-metalowe są w wielu przypadkach kluczowe dla właściwego funkcjonowania maszyn i urządzeń. Nie obędzie się bez nich przemysł motoryzacyjny, lotniczy, maszynowy czy wydobywczy. Można wymienić wśród nich chociażby pierścienie uszczelniające wałki obrotowe, wibroizolatory oraz łączniki sprężyste przenoszące różne rodzaje obciążeń (stosowane również w budownictwie i konstrukcjach mostów).
Połączenie uzyskiwane pomiędzy gumą a metalem musi charakteryzować się odpowiednią trwałością i wytrzymałością, aby przetrwać okres eksploatacji elastycznej części wyrobu. Dlatego należy skrupulatnie zaprojektować cały detal, jak i element metalowy, aby uniknąć nadmiernych naprężeń miejscowych. Warto mieć na uwadze, że w tego typu wyrobach zawsze będą występowały naprężenia, spowodowane chociażby skurczem gumy podczas chłodzenia po procesie wulkanizacji w wysokiej temperaturze. Skurcz technologiczny elementu gumowego będzie różny, w zależności od rodzaju używanego kauczuku, twardości mieszanki czy stopnia jej wypełnienia. Z tego powodu zmieniać się będzie też stosunek współczynników rozszerzalności cieplnej gumy i metalu.
Niezwykle istotne dla trwałości podzespołów gumowo-metalowych jest środowisko, w którym będą one pracować. Wulkanizaty charakteryzują się bowiem zróżnicowaną odpornością na działanie olejów i smarów, czy też różnorakich związków chemicznych, w zależności od zastosowanego kauczuku. Substancje chemiczne przenikające przez gumę mogą osłabić integralność warstwy wiążącej ją z metalową powierzchnią i doprowadzić do uszkodzenia detalu. Poważnym problemem może być korozja elementów metalowych związana z pracą w środowisku agresywnym, jak również wynikająca z niewłaściwego przygotowania ich powierzchni do połączenia z gumą.
Gumę z metalami możemy łączyć "na zimno" lub "na gorąco". Metoda "na zimno" dotyczy gumy zwulkanizowanej i obejmuje zastosowanie klejów chloroprenowych, epoksydowych lub cyjanoakrylowych. Na rynku dostępne są też wyroby (np. tulejowe elementy sprężyste typu silentblock), w których połączenie utrzymywane jest również wskutek naprężeń wstępnych ściskających i siły tarcia między tymi materiałami. Zazwyczaj jednak stabilne wiązanie między metalem a gumą uzyskuje się w podwyższonej temperaturze, w procesie wulkanizacji.
Historycznie ujmując, najstarsza metoda łączenia gumy z metalem "na gorąco" obejmowała wykorzystanie ebonitu (twardego materiału wytwarzanego metodą wulkanizacji siarkowej, zawierającego ok. 30% siarki). Mieszanek i klejów ebonitowych używa się jeszcze do zabezpieczania urządzeń i konstrukcji przemysłowych przed korozją i działaniem czynników chemicznych.
W połowie XIX w. odkryto, być może przypadkowo, że w trakcie wulkanizacji kauczuk naturalny wiąże się z mosiądzem. Ta metoda łączenia gumy z metalami stosowana jest do dziś. Stosuje się ją w celu zwiększenia przyczepności między stalowymi kordami wzmacniającymi a gumą w oponach radialnych. Najczęściej powleka się stal warstwą mosiądzu o nominalnej zawartości 70% miedzi. Podczas procesu wulkanizacji gumy powstaje silne wiązanie między powierzchnią mosiądzu a gumą. Spoiwo to jest bardzo trwałe, odporne na wysoką temperaturę i obciążenia dynamiczne. Inne sposoby łączenia obejmowały stosowanie klejów chlorokauczukowych, poliizocjanianów oraz żywic syntetycznych.
Przełom nastąpił w połowie lat 50. XX w., kiedy to w laboratoriach firmy Hugson Chemicals (przekształconej później w Oddział Produktów Chemicznych amerykańskiej firmy Lord Corporation) wynaleziono preparat Chemlok 220 - pierwszy z nowoczesnych, odpornych na wilgoć, środków wiążących. Trafił on na rynek Stanów Zjednoczonych w 1956 r., a na europejski w 1959 r., gdzie był sprzedawany i produkowany przez firmę Henkel pod nazwą "Chemosil".
Aż do wczesnych lat 90. kleje tego typu były opracowywane prawie wyłącznie na bazie rozpuszczalników organicznych - metanolu, metyloetyloketonu, octanu etylu. Ze względu na konieczność ograniczenia emisji lotnych związków organicznych (VOC) komercjalizowana jest coraz większa liczba produktów wodorozcieńczalnych.