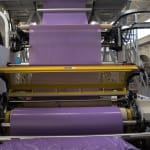
Przetwórstwo tworzyw to złożony, skomplikowany proces. Zawsze byłam pod dużym wrażeniem funkcjonalnych możliwości urządzeń przetwórczych i rezultatów uzyskiwanych dzięki ich wykorzystaniu. Wraz z postępem technologicznym oraz wprowadzaniem na rynek nowych rozwiązań nastąpił również dynamiczny rozwój większości gałęzi przemysłu. W branży zajmującej się wytwarzaniem i obróbką tworzyw sztucznych pojawiło się wiele ciekawych innowacji, które na dobre odmieniły różne procesy produkcyjne. Jednym z wartych uwagi zagadnień jest z pewnością wytłaczanie tworzyw - metoda stosowana aktualnie na bardzo szeroką skalę.
Wytłaczanie ma wśród sposobów przetwórstwa tworzyw polimerowych największe znaczenie, gdyż przetwarza się dzięki niemu ponad 50% produkowanych materiałów. Wbrew pozorom nie jest to proces prosty do przeprowadzenia w praktyce. Wiele razy miałam okazję się przekonać, że już samo urządzenie do wytłaczania jest obiektem trudnym do sterowania. Problemy mogą wyniknąć już w układzie uplastyczniającym wytłaczarki lub w procesie formowania materiału polimerowego; często jest też tak, że kłopoty generowane są przez czynniki niezależne od przetwórcy (np. wahania napięcia zasilającego czy też agresywne warunki panujące w maszynie, takie jak wysoka temperatura, duże ciśnienie, znaczne naprężenia ścinające oraz obecność różnych napełniaczy), które powodują przyśpieszone zużycie maszyn przetwórczych.
Według najbardziej popularnej definicji, wytłaczanie to proces technologiczny formowania półproduktów lub gotowych wyrobów, polegający na wciskaniu uplastycznionego tworzywa przed dyszę wytłaczarki, która nadaje gotowy kształt formowanemu przekrojowi. Zgodnie z innym wyjaśnieniem, przez pojęcie wytłaczania rozumie się ciągły proces otrzymywania wyrobów lub półwyrobów (w postaci profili, płyt lub folii) z tworzyw polimerowych, polegający na uplastycznieniu materiału w układzie uplastyczniającym wytłaczarki, a następnie jego ukształtowaniu poprzez wyciskanie przez odpowiednio ukształtowany ustnik znajdujący się w głowicy. W wielkim skrócie, chodzi tu o wytwarzanie elementów z tworzyw sztucznych i nadawanie im określonych wymiarów oraz kształtów. Osiąga się przy tym wydajność powyżej 1 tys. kg/h, a materiałem wyjściowym są tworzywa w postaci granulatu, proszku, płatków lub wiórów.
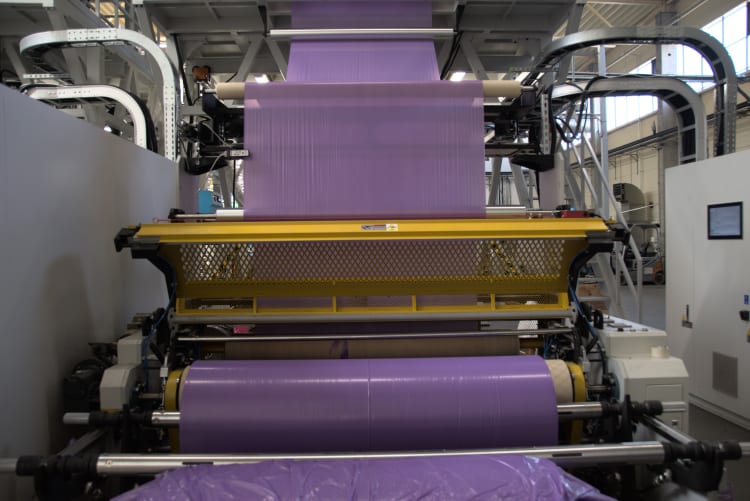
fot.: Linia do wytłaczania w firmie Polipak
Proces wytłaczania prowadzi się z 2 powodów. Po pierwsze, w celu formowania - uplastyczniony materiał na skutek dużego ciśnienia wytworzonego w układzie uplastyczniającym wytłaczarki jest przeciskany przez ustnik, który nadaje żądany kształt formowanemu tworzywu. Do procesów formowania materiałów jednorodnych stosowane są zwykle wytłaczarki jednoślimakowe. Do wytłaczania tworzyw wrażliwych termicznie (jak np. PVC) stosuje się również wytłaczarki dwuślimakowe przeciwbieżne lub planetarne, natomiast do formowania tworzyw modyfikowanych oraz kompozytów polimerowych - wytłaczarki dwuślimakowe współbieżne. Po drugie, w celu mieszania; wytłaczarki (głównie dwuślimakowe współbieżne, a w mniejszym stopniu także przeciwbieżne) są bowiem bardzo dobrymi urządzeniami mieszającymi.
Jak odbywa się proces wytłaczania?
Tworzywo polimerowe, np. w postaci granulatu, podawane jest do leja zasypowego wytłaczarki, skąd grawitacyjnie lub za pomocą odpowiednich podajników ślimakowych transportowane jest do cylindra. W cylindrze, w wyniku ciągłego ruchu obrotowego ślimaka, materiał jest transportowany w kierunku głowicy. W pewnym momencie tworzywo dostaje się do ogrzewanej strefy cylindra, gdzie ulega stopieniu, a następnie homogenizacji materiałowej i termicznej. Jednorodny stop podawany jest z odpowiednią prędkością do głowicy, gdzie materiał jest formowany przyjmując kształt ustnika. Wytłoczka jest chłodzona, a później cięta na odcinki o odpowiednim wymiarze lub nawijana na bębny, szpule itp.
Zastosowanie wytłaczania
Wytłaczanie jest jedną z najbardziej rozpowszechnionych metod przetwórstwa tworzyw polimerowych, znajdującą zastosowanie przede wszystkim w produkcji różnego typu rur, płyt, taśm czy folii. Ponadto, proces wykorzystuje się do wytwarzania różnego rodzaju pojemników i butelek oraz do powlekania kabli elektrycznych. Wytłaczarki są obecne w wielu gałęziach przemysłu. Używa się ich w obróbce metali, tworzyw sztucznych, materiałów ceramicznych; spotykane są też często w branży spożywczej oraz farmaceutycznej. Przedmioty, które otaczają nas w codziennym życiu (m.in. profile, parapety) to produkty otrzymywane właśnie przy zastosowaniu wytłaczarek. Warto zatem bliżej przyjrzeć się tym maszynom.
Urządzenie do wytłaczania
Wytłaczarka składa się z 3 podstawowych układów: napędowego, sterowania i plastyfikującego. Zwykle dodatkowo posiada specjalny zasobnik na surowiec (np. podajnik wolumetryczny lub grawimetryczny), a także szereg komponentów pomocniczych. W procesie wytłaczania bardzo ważną rolę odgrywa układ plastyfikujący, który stanowi istotny element każdej wytłaczarki. Składa się on ze ślimaków i cylindra. Wyróżniamy kilka rodzajów ślimaków: stożkowy, równoległy, współbieżny i przeciwbieżny. Konkretny typ dobierany jest adekwatnie do specyfiki przetwarzanego surowca; ślimak odpowiada bowiem za jakość i konsystencję uzyskanego tworzywa. Bierze też udział w uplastycznianiu materiału oraz powoduje jego homogenizację, czyli dokładne wymieszanie składników w celu uzyskania jednorodnej masy.