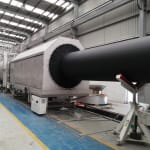
Wytłaczanie jest jednym z najczęściej spotykanych procesów technologicznych, a najbardziej znanym rodzajem maszyn do przetwórstwa tworzyw sztucznych są wytłaczarki. Są to zarazem jedne z najbardziej ekonomicznych i ekologicznych maszyn, jakie służą do przetwórstwa tworzyw, gdzie materiałem wyjściowym są granulaty, proszki lub mieszanina otrzymana według odpowiednich receptur, w odpowiedni sposób dozowane do wytłaczarki.
Wytłaczarka jest głównym elementem w procesie ekstruzji. Służy ona do dostarczania w sposób ciągły i stabilny odpowiedniej ilości uplastycznionego, homogenicznego tworzywa. Głowica (wymienna) jest urządzeniem formującym, mogącym nadawać wyrobom pożądane formy i kształty. Niezbędny jest także układ chłodzący i odbierający, niekiedy również rozdrabniający (gdy proces wytłaczania ma służyć do otrzymania homogenicznego granulatu). Masa tworzywa jest dostarczana lejem zasypowym do ślimaka, który obraca się w strefowo grzanym cylindrze. Tam tworzywo topi się głównie przez tarcie, czasem ewentualnie odgazowuje, ulega ujednorodnieniu przez ścinanie oraz spręża się. Działanie transportujące zachodzi wskutek występowania sił tarcia tworzywa względem ścian cylindra i ślimaka. Często za wytłaczarką znajduje się odciąg wyposażony w chłodzenie zimnym powietrzem, tak aby pręt otrzymany z wytłaczarki schłodzić poniżej temperatury mięknienia tworzywa. Kolejno materiał wprowadzany jest do granulatora, skąd odbierany jest do pojemnika. Czasem w celu szybszego odbioru ciepła od wytłaczanego tworzywa stosuje się wannę wypełnioną wodą i wówczas potrzebna jest także suszarka, która osusza materiał przez wprowadzeniem go na frez (do granulatora).
Podział wytłaczarek
Podziału wytłaczarek można dokonać ze względu na różne kryteria. Za pomocą diagramu przedstawiono ten, który uwzględnia liczbę ślimaków znajdujących się w maszynie.
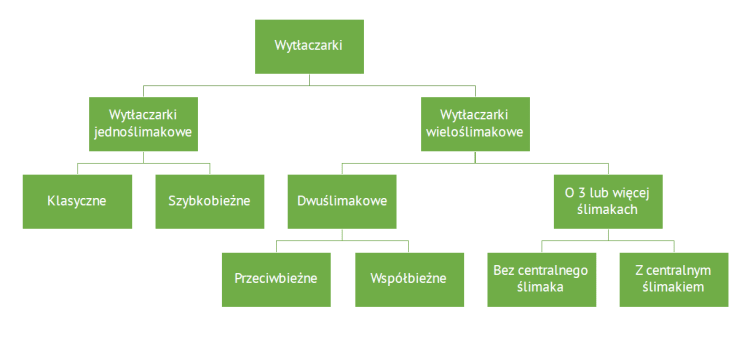
Wytłaczarki jednoślimakowe (klasyczne) to najczęściej stosowany typ maszyn; mają one długość ślimaków rzędu 20-36 D. Ich prędkości obwodowe przy przetwórstwie tworzyw stabilnych termicznie wynoszą 0,5-0,8 m/s, a dla materiałów niestabilnych cieplnie - ok. 0,3 m/s. Na rynku wytłaczarek jednoślimakowych obserwuje się tendencje do produkcji maszyn specjalistycznych, przeznaczonych do przetwórstwa określonego tworzywa i otrzymywania konkretnego wyrobu. Wytłaczarki takie charakteryzują się przede wszystkim dużą wydajnością wytłaczania oraz zapewniają otrzymywanie wyrobów o optymalnych właściwościach.
Wytłaczarki szybkobieżne (adiabatyczne) pracują z dużymi szybkościami obrotowymi (do 700 obr./min., prędkości obwodowe do 4 m/s). Ich ślimaki są tak skonstruowane, że topienie tworzywa następuje wyłącznie za pomocą tarcia (energii ścinania). Maszyny te są proste pod względem budowy i nadają się do przetwórstwa tworzyw niewrażliwych na działanie temperatury.
Wytłaczarki dwuślimakowe podzielić można ze względu na różne kryteria, z których najważniejszym jest kierunek obrotu ślimaków: w maszynach współbieżnych ślimaki obracają się w tym samym kierunku, podczas gdy w przypadku przeciwbieżnych ślimaki obracają się w kierunkach przeciwnych.
Ze względu na stopień zazębienia zwojów obu ślimaków wytłaczarki te można podzielić też na zazębiające się całkowicie, częściowo lub niezazębiające się. W przemyśle zastosowanie znalazły głównie wytłaczarki współbieżne i przeciwbieżne o zwojach zazębiających się nieszczelnie, w których występują luzy międzyzwojowe spełniające ważną rolę w procesie uplastyczniania, szczególnie w procesach homogenizacji materiałowej. Wśród wytłaczarek niezazębiających się praktyczne znaczenie posiadają wyłącznie wytłaczarki przeciwbieżne. Kształty i wymiary kanałów oraz zwojów jednego ślimaka są tutaj ściśle zależne od kształtów i wymiarów drugiego.
Inne ważne kryterium podziału to krotność zwojów ślimaka - wśród wytłaczarek dwuślimakowych znane są wytłaczarki jedno-, dwu- lub trójzwojowe. Ponadto wytłaczarki dwuślimakowe mogą się różnić kształtem rdzeni ślimaków; wytłaczarki dwuślimakowe produkowane są w wersjach walcowych i stożkowych. Wytłaczarki o wydajności do 200-300 kg/h wykonywane są najczęściej jako stożkowe, natomiast wytłaczarki o większej wydajności produkuje się jako walcowe.
Wytłaczarki o 3 lub więcej ślimakach pracują w wersjach przeciwbieżnych i znajdują zastosowanie, podobnie jak wytłaczarki przeciwbieżne, w przetwórstwie materiałów wrażliwych termicznie.
Kluczowymi kryteriami doboru podstawowych parametrów dla wytłaczarek są: rodzaj przetwarzanego tworzywa, jego forma, stopień zabrudzenia i zawilgocenia czy wielkość i jakość uzyskiwanego granulatu. W przypadku tworzyw homogenicznych, z reguły wystarczające są wytłaczarki jednoślimakowe, które są ciągle najczęściej stosowanymi w wytłaczaniu tworzyw sztucznych. Dla potrzeb obróbki lekko zadrukowanych materiałów folii jak i przemiałów sprawdzą się jednoślimakowe wytłaczarki z dołączonym kompaktorem. W przypadku przetwarzania wyłącznie sypkich przemiałów, najlepszym rozwiązaniem może okazać się wykorzystanie wytłaczarki z koszem zasypowym. Wytłaczarki dwuślimakowe współbieżne, pracujące przy znacznie wyższych prędkościach obrotowych, znajdują zastosowanie głównie w bezpośrednim wytwarzaniu gotowych półwyrobów z tworzyw modyfikowanych i kompozytów polimerowych. Wytłaczarki dwuślimakowe przeciwbieżne, ze względu na niewielkie prędkości obrotowe ślimaków oraz niewielkie siły ścinające występujące w układzie uplastyczniającym, używane są głównie w przetwórstwie tworzyw o małej stabilności cieplnej, takich jak kauczuki czy PVC.