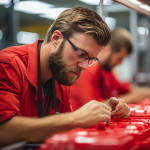
Obecna sytuacja na rynku AGD przypomina tę z lat 2008-10. Wszyscy szukają tak zwanego CCC: Cena Czyni Cuda. Udział surowca w cenie komponentu wynosi obecnie 50%, a nawet 75%. Dlatego z punktu widzenia “wartości dodanej” pozostaje naprawdę niewielkie pole do zagospodarowania. Czy na pewno musi to tak wyglądać? Czy są inne obszary budowania przewagi nad konkurencją?
W 2024 roku sytuacja prezentuje się w taki sposób, że nawet dostawcy chcą wzrostu cen komponentów, co pozwoli zwiększyć udział wartości dodanej w cenie. Poprzez tę wartość dodaną rozumiemy nowatorskie, kreatywne podejście i/lub pomysł na poprowadzenie całego projektu od A do Z. Jednak na skutek dominacji ceny, producenci przede wszystkim szukają alternatyw, czyli np. migrują swój biznes tam, gdzie rośnie na niego zapotrzebowanie, gdzie równolegle jest w stanie utrzymać obecną cenę, a dodatkowo dostawcy potrafią zaoferować rozwiązanie, które jeszcze bar-dziej “zoptymalizuje” cenę poszczególnych elementów.
- Wyraźnie widać, że surowce stały się najważniejsze. Cena oryginalnego ABS wynosi 1,6-1,7 euro, a regranulatu (w pełni transparentnego oraz w najwyższej jakości) 1,2-1,3 euro. To różnica aż 40 eurocentów na kilogramie. Ma to bezpośredni wpływ na końcową cenę komponentu o kilkadziesiąt procent. Dokładnie tak samo jest z polipropylenami, podobnie z polistyrenami, tworzywami technicznymi. Do tego dochodzą odgórne regulacje (takie jak ROP). Z kolei na rynku w Polsce pojawia się kolejna komplikacja: jest on zalewany naprawdę bardzo tanimi polipropylenami – mówi Marek Bądkowski, ekspert przetwórstwa tworzyw sztucznych, doradca i zarządzający firmami z tego rynku.
Jak w tym wszystkim myśleć o konkurowaniu czymś więcej niż ceną? Można znaleźć na rynku dostawców, którzy oferują bardzo dobre ceny surowców z recyklingu w stosunku do oryginałów. A przy tym dostarczają bardzo wysoką jakość i powtarzalność. Do tego - co jest kluczowe - można u nich szukać odpowiednich zamienników lub technologii, które w nieoczywisty sposób korzystnie wpłyną na cenę. Tutaj spektrum możliwości staje się naprawdę bardzo szerokie dzięki rozwiniętej myśli R&D. To właśnie te departamenty mają coraz więcej do powiedzenia i warto być otwartym na ich pomysły.
Jeśli chce się poważnie myśleć o zamianie produktów prime’owych na te z recyklingu, to trzeba podejść do tego procesowo. Biorąc pod uwagę wymagania techniczne dla konkretnej aplikacji należy dobrać odpowiednie technicznie tworzywo recyklingowane, a równolegle zastanowić się nad optymalizacją konstrukcji detalu pod możliwości techniczne tego tworzywa - tam gdzie jest to niezbędne. Ta druga kwestia wiąże się kosztami modyfikacji formy wtryskowych, co (szczególnie w obecnej sytuacji) jest rozwiązaniem bardzo niepożądanym. Na rynku działa też wielu producentów materiałów recyklingowych o niskich i bardzo niskich cenach, ale są to materiały mogące mieć potencjał w prostych, niewymagających aplikacjach.
Aby wejść na wyższy poziom trzeba wyposażyć firmę produkcyjną w odpowiednie narzędzia. Podstawową rolę w komponowaniu właściwych tworzyw i kontroli ich parametrów spełnia laboratorium, które jest nieodzownym departamentem wspierającym pracę R&D i technologię produkcyjną.
- CCC to pociągający skrót, ale w świecie tworzyw w większości przypadków nic nie jest proste. W wielu aplikacjach wymiana tworzyw z primów na recyklingowe musi być potraktowana kompleksowo, a rezultat (czyli efekt finansowy tych zmian) będzie zależał od wspólnej pracy projektantów detali i projektantów tworzyw. Jak to może wyglądać w praktyce? Bardzo mocno zacieśniliśmy współpracę inżynierów z R&D i zespołu laboratorium i w ten sposób opracowaliśmy materiały mogące być stosowane m.in. w przemyśle AGD i samochodowym. Głównym celem było zbalansowanie ceny i jakości do wymagań rynku. Podstawową kwestią - oprócz wymagań formalnych - jest stabilność tworzyw w procesie przetwórstwa. Z jednej strony cena tworzywa jest obecnie kryterium najważniejszym, z drugiej brak stabilności procesu wtrysku powoduje przestoje w pracy maszyn, co przekłada się na większe zużycie zasobów (ludzkich i maszynowych). To w konsekwencji oznacza zwiększone koszty wytworzenia. Dlatego na bazie rPA, rPP, rPC stworzyliśmy serię produktową Terez, która powyższy cel perfekcyjnie spełnia - mówi Waldemar Purc, Dyrektor Zarządzający TEREZ Performance Polymers i Ter Plastics Polska.
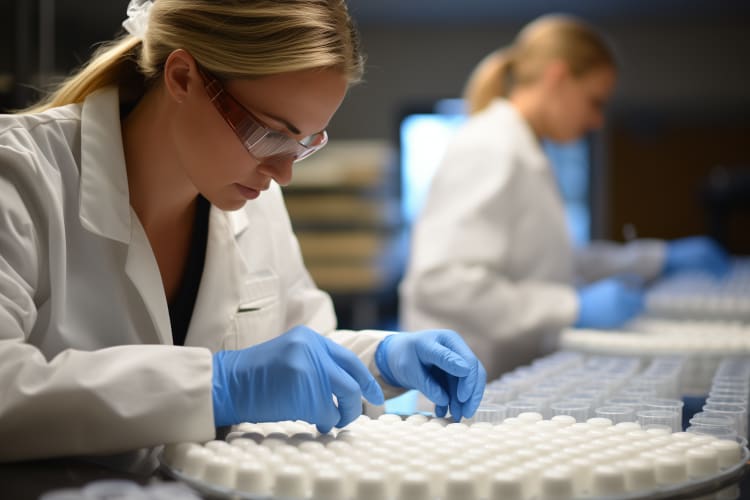
Posiadanie działu badań i rozwoju w branży przetwórstwa tworzyw sztucznych wyrosło na kluczowy czynnik budowania konkurencyjności firmy. Do niedawna w większości międzynarodowych firm dział R&D funkcjonował niezależnie od działów zakupów odpowiedzialnych za zakupy produkcyjne. Każdy z nich miał inne cele: zakupy miały obniżać ceny poprzez negocjacje z poddostawcami, zaś R&D wprowadzać nowe rozwiązania, które budują wartość dodaną produktu albo zmieniać konstrukcję poszczególnych podzespołów w kierunku obniżenia ceny. Rozdział ten często generował problemy pod tytułem “kto wygenerował oszczędność?”, “kto zrealizował cel?”. Obecnie działy R&D stają się głównym decydentem i motorem zdobywania rynku.
- Wydaje się to zrozumiałe, ale z drugiej strony R&D nie istnieje bez odpowiedniego wsparcia. W obecnej sytuacji, poza „rewolucyjnym rozwiązaniem”, znaczący wpływ ma łańcuch dostaw. Działy zakupów funkcjonują w trybie ciągłych poszukiwań, a sukces firmy często zależy bezpośrednio od nich. Przy dużych zmianach geopolitycznych, nowych regulacjach i dyrektywach, konieczne jest bardzo dobre rozeznanie nie tylko w cenie, ale i dostępności, czasie dostawy i kierunku rozwoju rynku w danym segmencie. Zakupy są i będą prawą ręką R&D w rozwoju biznesu - dodaje Marek Bądkowski.