A czy mógłby pan przedstawić obecną kondycję Canexpolu w liczbach?
Pomimo pojawiających się na świecie trudności, takich jak pandemia, inflacja, problemy surowcowe, kryzys energetyczny itp., Canexpol potrafi dostosować się do zmieniającej się sytuacji rynkowej, zachowując konkurencyjność i stale poszerzając rynki zbytu. Z dumą mogę powiedzieć, że aktualna kondycja Canexpolu przedstawia się imponująco.
Liczba pracowników tworzących zespół Canexpol to obecnie ponad 300 osób; w ciągu ostatnich 5 lat powiększyliśmy 2-krotnie powierzchnię produkcyjno-magazynową. Całkowita powierzchnia produkcyjna wynosi 9 tys. m2, zaś powierzchnia magazynowa 11 tys. m2.
Ilość produkowanych wyrobów w ujęciu rocznym to 61 156 000 sztuk; w okresie ostatnich 5 lat odnotowaliśmy prawie 2-krotny wzrost sprzedaży, a na przestrzeni ostatnich 20 lat ten wzrost jest 10-krotny… A co najważniejsze, nieustannie poszerza się grono zadowolonych klientów.
Jak wygląda wasz park maszynowy?
Dysponujemy kilkudziesięcioma wtryskarkami renomowanych europejskich firm, takich jak Arburg i KraussMaffei. Długoletnie doświadczenie tych producentów gwarantuje powtarzalność i jakość wytwarzanych produktów. Maszyny wyposażone są w roboty, które zapewniają pracę w cyklu automatycznym, odbiór wyprasek z formy i umieszczenie ich na transporterach taśmowych znajdujących się przy wtryskarce. Dodatkowym atutem robotów jest możliwość umieszczania zaprasek w formach, np. zbrojenie metalowymi elementami.
Zróżnicowanie wielkości maszyn ze względu na siłę zwarcia od 40 do 650 ton oraz wagę wtrysku od kilku gramów do max. 3 kilogramów zapewnia nam duże możliwości produkcyjne. Na naszych wtryskarkach możemy przetwarzać oprócz najbardziej znanych tworzyw typu PP, PE, również tworzywa techniczne: PC, PA, POM, ABS, SBC, PMMA, PC+ABS, TPU, TPV oraz dzięki wzmocnionym układom plastyfikacji tworzywa zbrojone np. włóknami szklanymi.
Co zatem, w oparciu o wasze doświadczenie, zespół i urządzenia oferujecie swoim klientom?
Jak już wcześniej wspomniałem, oferujemy naszym klientom współpracę "od pomysłu do produktu". Nowoczesny park maszynowy umożliwia nam realizację produkcji zgodnie z wymogami, a nasz zespół doświadczonych specjalistów R&D, mających wieloletnie doświadczenie we wdrażaniu do produkcji wyrobów z tworzyw sztucznych, gwarantuje pełne wsparcie i nadzór oraz odpowiedzialność za realizację projektu.
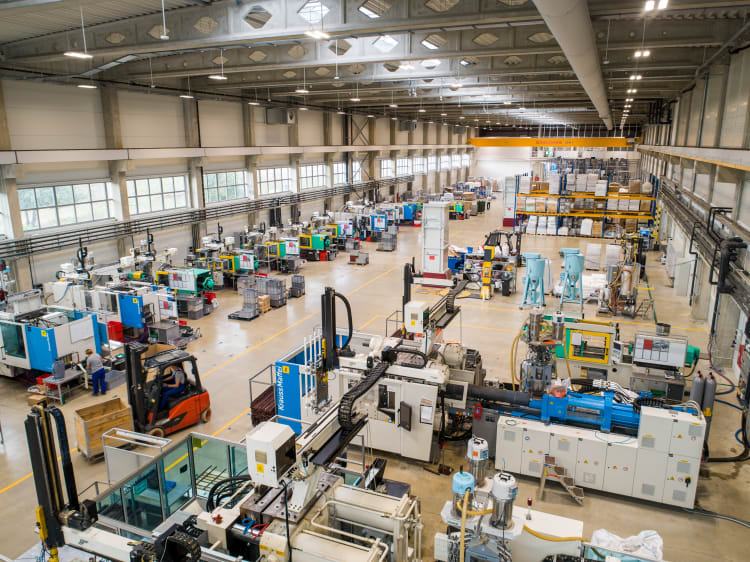
Proszę powiedzieć, jak wygląda w praktyce współpraca z waszymi klientami. Załóżmy, że mam tylko pomysł, a nie gotowy projekt. Mogę się do was zgłosić?
To bardzo trafne pytanie. Rzeczywiście, często się zdarza, że potencjalny klient zgłasza się do nas w celu wyceny projektu nieposiadającego jeszcze ostatecznego kształtu, lub którego projekt 3D jeszcze nawet nie istnieje. Jeżeli jednak klient dysponuje pełną wiedzą co do wymaganej funkcjonalności, zna wszystkie pozostałe wymagania dotyczące wyrobu, projekt ilościowo i jakościowo jest optymalny dla produkcji w technologii wtrysku oraz istnieje świadomość kosztów wdrożenia i produkcji w kontekście potencjału rynku, to mamy dużą szansę na rozpoczęcie współpracy zmierzającej w pierwszym etapie do doprecyzowania kwestii designu umożliwiającego przedstawienie oferty na wdrożenie i produkcję.
To znacznie ułatwia podejmowanie decyzji waszym klientom. A jak wygląda cały proces współpracy?
Każdy klient wymaga indywidualnego podejścia. Przeprowadzenia szczegółowego wywiadu czy też spotkania, na którym poznamy dokładnie jego potrzeby oraz dowiemy się, w jakiej fazie dany projekt się znajduje, a dzielimy go z reguły na 6 faz.
Pierwszą fazą jest stworzenie designu. Jest niezmiernie istotne, aby tworząc projekt przewidywać już na tym etapie, w jakiej technologii ma ostatecznie być wykonany wyrób i dostosować kształt oraz projektowane funkcjonalności do możliwości, ale też ograniczeń danej technologii.
Następny etap to utechnologicznienie. Jest to w zasadzie rozwinięcie fazy pierwszej o dokładną analizę wszystkich aspektów konstrukcji wpływających na zastosowane rozwiązania form wtryskowych i ich koszt, a także na późniejszy przebieg procesu wtrysku, jego optymalizację kosztową i jakościową oraz optymalizację pakowania i transportu.
W dalszym kroku wykonujemy prototyp i dokonujemy walidacji konstrukcji wyrobu. Właściwie dobrana technologia wydruku 3D pozwala stworzyć prototyp, dzięki któremu będzie można wykonać niezbędne testy i ostatecznie zatwierdzić jego design.
Następnie możemy już zaprojektować formę wtryskową. Jej konstrukcja weryfikowana jest w oparciu o opracowane przez nas założenia konstrukcyjne, gdzie w pełni określona jest wymagana specyfikacja narzędzia.
Oczywiście istotnym elementem jest nadzór nad wykonaniem wszystkich elementów formy wtryskowej, ich montaż oraz próby technologiczne, co gwarantuje otrzymanie wypraski zgodnie z oczekiwaniami.
Zwieńczeniem całego procesu współpracy jest rozpoczęcie produkcji seryjnej, zgodnej z uzgodnionymi kryteriami jakościowymi zaakceptowanymi przez obie strony.
Nasze uczestnictwo w każdej z przedstawionych faz projektowych gwarantuje ostateczny sukces przedsięwzięcia. Oczywiście w ramach współpracy oferujemy także szereg innych usług dopasowanych do potrzeb klienta, tj. możliwość montażu podzespołów z dostarczonymi elementami, znakowanie, zgrzewanie ultradźwiękowe, pakowanie, magazynowanie i wysyłkę.