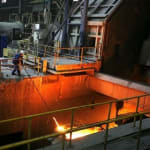
Zdaniem ekspertów ze stowarzyszenia PlasticsEurope stosowana tu technologa spalania odpadów z tworzyw sztucznych w piecach hutniczych modelowo wręcz wpisuje się w strategię oszczędzania surowców naturalnych w przyszłości.
Opisana technologia uruchomiona został jako projekt pilotażowy w 2003 r. Prowadzona w hucie produkcja żelaza odbywa się w piecu hutniczym o objętości 4000 m3. Tlenki żelaza podawane są od góry. W dolnej części pieca podawane są paletyzowane odpady z tworzyw sztucznych, a temperatura w tej części sięga nawet 2300 st. C. W tych warunkach materiał organiczny ulega gazyfikacji z wytworzeniem gazu syntezowego, zawierającego m.in. tlenek węgla. Gaz ten redukuje tlenki podczas ich wędrówki w dół pieca. Temperatura gazu syntezowego wynosi 900 - 1200 st. C, więc tym samym powstające żelazo jest w postaci stopionej. Ciekła surówka gromadzi się na dole pieca, skąd jest okresowo odbierana. Wydajność pieca hutniczego to 10 tys. ton dziennie.
Odpady z tworzyw sztucznych są w tej technologii w absolutnym centrum zainteresowania. Jeden z reaktorów procesu wielkopiecowego został zbudowany, aby możliwe było utylizowanie odpadów z tworzyw sztucznych przy jednoczesnej produkcji surówki żelaza, co umożliwiło jednocześnie oszczędności rzędu 150 tys. ton ropy naftowej rocznie. Zazwyczaj tlenek węgla jako czynnik redukujący otrzymywany jest zazwyczaj z ropy naftowej, węgla i koksu. Tymczasem te paliwa kopalne można zastąpić zużytymi tworzywami sztucznymi, efektywnie oszczędzając surowce naturalne.
W ramach technologii czynnik redukujący otrzymywany jest z odpadów z tworzyw sztucznych, pozyskiwanych ze zbieranych selektywnie odpadów opakowaniowych z gospodarstw domowych oraz z odpadów przemysłowych, a także z pozostałości po strzępieniu pojazdów wycofanych z eksploatacji lub ze zużytego sprzętu elektronicznego. Po wstępnej obróbce odpady są mieszane, a następnie odpowiednio aglomerowane i peletyzowane. Czynnik redukujący w formie pelet jest transportowany rurociągami do przesyłu na duże odległości i podawany do pieca hutniczego bezpośrednio poniżej strefy redukcji.
Huta Voestalpine dysponuje możliwością przerabiania rocznie 220 tys. ton odpadów z tworzyw sztucznych, co przyczynia się do oszczędzania zużycia ropy naftowej. Pierwsze próby, przeprowadzone dla ilości 30 tys. ton odpadów w formie pelet granulatu lub aglomeratu, okazały się zadowalające i projekt został rozszerzony do obecnego potencjału 220 tys. ton odpadów rocznie.