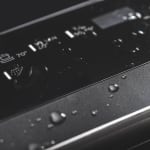
Granulaty. Słowo, które wywołuje skrajne emocje. Chyba jednak wszyscy zgadzają się co do tego, że są one wyzwaniem. Do tego dochodzi Dyrektywa ROP, potrzeby wynikające z korporacyjnych polityk ESG i naciski ze strony organizacji branżowych i klientów. Są jednak na rynku rozwiązania, które pokazują, że osiągnięcie pożądanego stanu pt. “więcej oszczędności + zachowanie jakości” jest możliwe.
Mimo wyzwania produkcyjnego, jakim jest regranulacja da się już znaleźć wypracowane standardy, studia przypadku i doświadczenia, z których można czerpać. Ważna jest też pewna techniczna kreatywność (oraz – co bardzo ważne – swoboda działania działu R&D), która pozwala łączyć technologie na różnych etapach łańcucha dostaw. W tym artykule pokazujemy przykład.
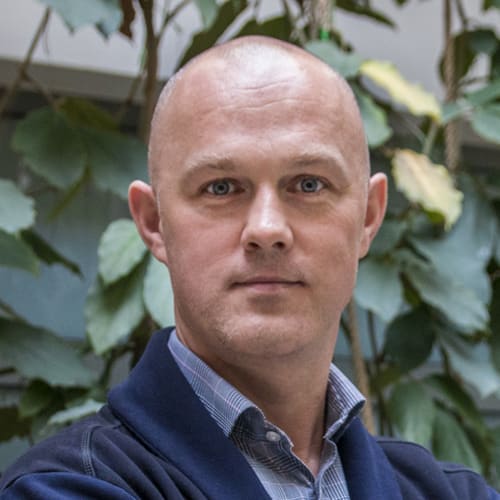
Marek Bądkowski
- Osią, technologią kluczową spinającą cały zamysł w jedno jest tu technologia sputteringu. W AGD można w ten sposób tworzywami zastąpić elementy metalowe w wielu estetykach: panelach kontrolnych, frontach drzwi w pralkach, zmywarkach, wyświetlaczach dotykowych, uchwytach itd. Przewagą tego rozwiązania jest brak inwestycji w narzędzia typu tłoczniki (również w momencie wykonywania modyfikacji) oraz ograniczenie łańcucha dostawców z kilku etapów metal-tworzywo-nadruk-złożenie do jednego dostawcy. W finale mamy poważne ograniczenie kosztów związanych z logistyką i jakością – mówi Marek Bądkowski, ekspert przetwórstwa tworzyw sztucznych, doradca i zarządzający firmami z tego rynku.
Na czym to polega w praktyce? Zamiast elementów metalowych do produkcji wykorzystuje się lżejsze elementy z tworzyw sztucznych pozyskiwane z recyklingu, na które następnie napyla się cienką warstwę dowolnego metalu (stali, srebra, złota). Przyjazność środowisku bierze się tu z tego, że odchodzimy od metalu na rzecz tworzyw, które są w całości przetwarzalne - każdy taki element można ponownie "zmielić" i wyprodukować jako zupełnie nowy, dowolny produkt. Za tym idzie zmniejszanie liczby dostawców, narzędzi, surowców, homologacji wyrobów, czyli mówiąc krótko: niższe koszty.
- Produkcja zorganizowana w ten sposób jest szybsza, zautomatyzowana, nie wymaga tworzenia całych parków maszynowych, hal produkcyjnych. Całość odbywa się na jednym, jeśli można tak powiedzieć "prostym" urządzeniu, które dodatkowo nie generuje takiej ilości odpadów i może być obsługiwane przez osoby bez specjalistycznego wykształcenia. Zastosowanie ma to nie tylko w AGD, ale też np. motoryzacji czy budownictwie – dodaje Marek Bądkowski.
Najważniejszy pierwszy krok, czyli od czego zacząć?
Wszystko to brzmi niezwykle atrakcyjnie. Żeby jednak taka produkcja stała się faktem, trzeba móc wykorzystać do niej tworzywa z odzysku, regranulaty, które sprostają konkretnym wymogom: przede wszystkim stabilności, powtarzalności i niskiej odpadowości. Wszystko zaczyna się od pozyskania samego tworzywa, które powinno mieć udokumentowane źródło pochodzenia. Wtedy następują kolejne etapy procesu pozwalające dostarczyć właściwe tworzywo do konkretnej aplikacji.
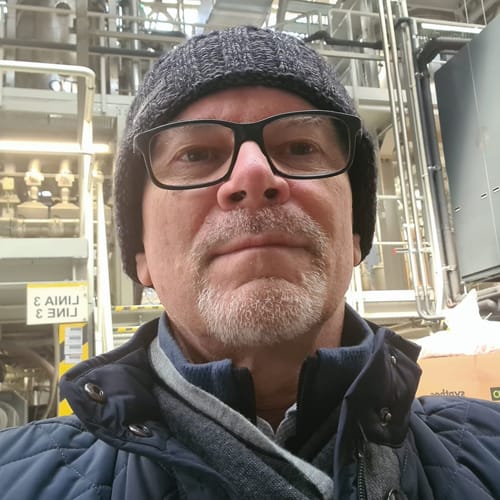
Waldemar Purc
- Finalny sukces zależy od dobrania właściwej receptury i utrzymywania reżimów procesowych. Po pozyskaniu odpowiedniej jakości składników, czyli tworzyw z recyklingu, trzeba je zbadać na wejściu i jak to robimy u nas, przypisać do odpowiednich grup jakościowych. To nam daje pewność w doborze właściwego procesu produkcyjnego. Na czym polega ta selekcja? Na analizie m.in. lepkości tworzywa, zawartość związków lotnych, metalu czy właściwości termicznych, jak TGA i DSC. Teoretycznie ciężko jest zbadać, ile cyklów życia ma za sobą dane tworzywo, ale w laboratorium udaje się zrobić to pośrednio - mówi Waldemar Purc, Dyrektor Zarządzający TEREZ Performance Polymers i Ter Plastics Polska.
Po osiągnięciu tego pułapu w produkcji często dochodzi kolejne wyzwanie – szczególnie w przypadku elementów estetycznych. – Poliamidy napełniane włóknem szklanym są bardzo pożądanym materiałem konstrukcyjnym. Jednak częstym problemem procesowym jest jakość powierzchni wtryskiwanego detalu: między innymi ze względu na widoczność włókien szklanych na powierzchni detalu estetycznego (np. na uchwycie drzwi do pralki jest to dyskwalifikujące). Jednak, mając do dyspozycji tworzywa wyprodukowane z materiałów recyklingowych o wysokiej powtarzalności jakościowej, można ten problem zminimalizować poprzez naniesienie w formie struktury, która w trakcie wtrysku odzwierciedla np. efekt drewna, skały, metalu - dodaje Waldemar Purc.
Wtedy przechodzi się do lakierowania. Na wypracowaną w powyższy sposób powierzchnię nanosi się konkretny lakier tzw. primer, który ma właściwości fizykochemiczne powierzchni wygenerowanej w sputteringu. Ma to przede wszystkim na celu zwiększenie wytrzymałości na różnego typu uszkodzenia mechaniczne, co odpowiednio się testuje.
- Pierwszy test to tzw. siatka nacięć, po których powierzchnia nałożona w ramach sputteringu i lakierowania nie powinna w żaden sposób odchodzić od wyprodukowanego elementu. Drugi test to tarcie środkiem czyszczącym z opiłkami metalu. Z kolei trzeci, najbardziej popularny, to test alkoholem. Na powłokę dozuje się alkohol, a następnie na różne sposoby trze, pociera etc. Cel oczywiście jest taki, aby nie było żadnego uszczerbku. Pewnym wyzwaniem zawsze są tzw. “wtrącenia” po naniesieniu lakieru. Są to drobne elementy, które są np. zasysane z powietrza w procesie lakierowania. Dobre lakiernie mają tych wtrąceń bardzo mało, ale bardzo rzadko zdarza się, aby nie było ich w ogóle. To też jest bardzo dobry sposób oceny jakości wykonania - dodaje Marek Bądkowski.
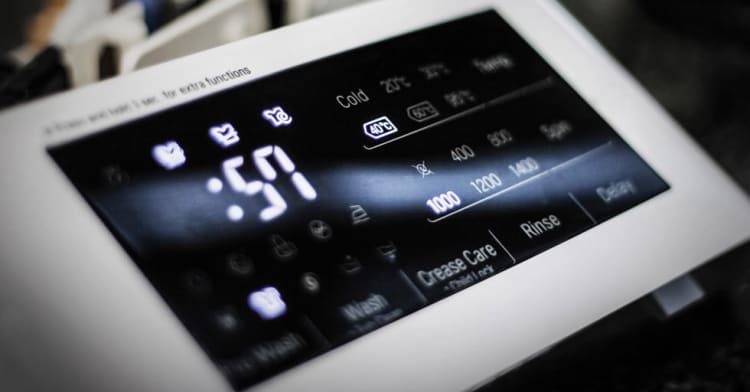
Efekt końcowy całości? Korzyści jest wiele, ale najbardziej rzuca się w oczy skrócenie łańcucha dostaw. Do niedawna większość procesów produkcyjnych wymagała ogromnej machiny logistycznej, nierzadko pomiędzy dwoma kontynentami. Przy wykorzystaniu powyższych technologii w wielu przypadkach – np. w elektronice, AGD, czy automotive – większość produkcji może odbywać się w ramach jednego kraju, a nawet jednej fabryki. Do tego dochodzi coraz bardziej powszechna automatyzacja i cyfryzacja, która pomaga w jednym miejscu wykonywać wszystkie procesy związane np. z wtryskiem tworzyw sztucznych w szerokim zakresie tonażu, wtrysku dwuskładnikowego, obtrysku, lakierowania, uszczelniania i montażu. Takie holistyczne podejście do produkcji, wykorzystując uczenie maszynowe, analizę danych i łączenie technologii pozwala krok po kroku dochodzić do miejsca, w którym obieg zamknięty nie będzie jawił się jako nieuchwytny mit czy science fiction.