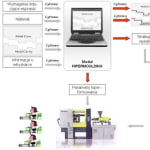
Przez trzy lata projekt Extreme Cycle Time Reduction of Injection Moulding Processes by using High Performance Injection Moulds and Moulding Processes, był realizowany przez konsorcjum ośrodków badawczo -rozwojowych, stowarzyszeń przemysłowych oraz małych i średnich przedsiębiorstw, działających w branży przetwórstwa tworzyw sztucznych.
Łącznie brały w nim udział 24 podmioty z Belgii, Hiszpanii, Holandii, Portugalii, Polski i Wielkiej Brytanii. Te polskie podmioty to firma Wadim Plast oraz Centrum Zaawansowanych Systemów Produkcyjnych CAMT z Politechniki Wrocławskiej, Towarzystwo Przetwórców Tworzyw Wielkocząsteczkowych z Częstochowy i Spółdzielnia Inwalidów Spamel. Projekt, który rozpoczął się jeszcze w grudniu 2004 r. opiewał na 4,4 mln euro.
Zdaniem uczestników właśnie dobiegł końca i skończył się sukcesem.
Wszystkie podmioty, które wchodziły w jego skład otrzymały oprogramowanie Hipermould związane z projektowaniem form wtryskowych z kanałami chłodzącymi konformalnymi. Oprogramowanie zostanie teraz sprawdzone w praktyce przemysłowej.
Na czym dokładnie polegał projekt Hipermould?
Był to projekt technologiczny, służący produkcji gniazd form wtryskowych. Jednym z jego głównych zadań było uzyskanie m.in. skróconego do minimum czasu chłodzenia oraz zminimalizowanie naprężeń tworzywa sztucznego w wypraskach.
Było to możliwe do osiągnięcia poprzez wykonanie w odpowiedni sposób kanałów chłodzących, przebiegających w jednakowej odległości od powierzchni gniazda. Pozwoliło to na szybkie i równomierne odprowadzenie ciepła z wypraski. Różnica polega tu na zastosowanej technologii w produkcji form.
Oto bowiem tradycyjna technologia polegała na wykonaniu kanałów chłodzących (rys. po lewej stronie) i wydrążeniu w bloku metalu kształtu, który odpowiada kształtowi wypraski. Główną wadą tej metody było nierównomierne odprowadzenie ciepła z wypraski, co w konsekwencji mogło prowadzić m.in. do nierównomiernych skurczów w wyprasce. Tymczasem w technologii Hipermoulding (rys. po prawej stronie) wykonanie kanałów chłodzących jest do zrealizowania poprzez zastosowanie metody przyrostowej (warstwa po warstwie) w produkcji gniazda. Uzyskuje się to poprzez spiekanie odpowiednio spreparowanych kryształków metalu za pomocą lasera w urządzeniu sterowanym komputerowo.