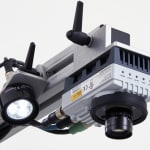
Odpady spożywcze stanowią wyzwanie na globalną skalę. FAO (Organizacja Narodów Zjednoczonych ds. Wyżywienia i Rolnictwa) szacuje, że każdego roku marnuje się aż 1,3 miliarda ton żywności. Przyczyny mogą być różne: od niezebranych plonów, przez towary uszkodzone i przeterminowane, aż po resztki z gospodarstw domowych. Na etapie produkcji i pakowania problem polega przede wszystkim na tym, że produkty w wadliwych opakowaniach trafiają na półki sklepowe, gdzie konsumenci odrzucają je z powodu defektów wizualnych. Zapobiega temu najnowocześniejsza technologia.
Każdemu z nas zdarzyło się zapewne podczas zakupów natrafić na paczkę sera w wadliwym opakowaniu. Wydawało się nieszczelne albo nadruk nie był idealny. Klient prawdopodobnie zostawi taki produkt na półce. Podobnie postąpi kolejna osoba, i w ten sposób paczka sera staje się odpadem spożywczym. Ich ilość tylko w Wielkiej Brytanii szacuje się na 480 tysięcy ton rocznie.
Konsumenci stają się coraz bardziej krytyczni, co ma wpływ na ich wzorce zakupowe. Opakowania zyskują na znaczeniu, stają się coraz bardziej kolorowe. Bezpieczne opakowanie zapobiega zepsuciu się produktu podczas transportu, zakupów i przechowywania. Lista pięciu najpoważniejszych defektów opakowań obejmuje: migrację/ługowanie, zanieczyszczenie, przyleganie/uszczelnienie, wady materiałowe i błędy w etykietowaniu. Technologia wizyjna pomaga producentom żywności w kontrolowaniu wyglądu opakowań i ich jakości na wczesnym etapie procesu produkcyjnego, zmniejszając ilość odpadów w handlu detalicznym i na liniach produkcyjnych.
Ograniczenie odpadów dzięki wykorzystaniu technologii
Przemysłowa technologia wizyjna wykorzystuje szybkie kamery o wysokiej rozdzielczości do wykrywania wad produktów - co może zapobiec marnotrawstwu żywności w większej skali. Przemysłowa technologia wizyjna istnieje od ponad 40 lat, ale w ciągu ostatnich 15-20 lat, dzięki szerokiemu rozpowszechnieniu zautomatyzowanej produkcji, staje się coraz popularniejsza.
Technologia znajduje zastosowanie w wielu zakładach produkcyjnych, począwszy od przemysłu motoryzacyjnego, poprzez elektronikę, aż do nauk przyrodniczych i farmacji. Duńska firma TriVision zdobyła bogate doświadczenie w tego typu rozwiązaniach dla sektora produkcji żywności i ma na koncie wiele efektywnych wdrożeń.
Stworzony przez Duńczyków kompletny system VisioPointer to rozwiązanie oparte na zaawansowanej technologii wizyjnej. System VisioPointer w pełni automatyzuje kontrolę szczelności opakowań, opakowań IML, etykiet, druku, grafiki oraz kodów kreskowych.
- Skandynawski gigant spożywczy Arla Foods od wielu lat jest naszym kluczowym klientem - mówi Ole K. Neckelmann, partner w TriVision. - Celem Arla Foods jest dostarczanie doskonałych jakościowo produktów. Firmie udało się ograniczyć liczbę przestojów produkcyjnych, związanych z problemami z jakością. Jednocześnie spadła liczba skarg klientów. To prawdziwy sukces, który firma osiągnęła zmniejszając jednocześnie ilość odpadów.
Kamery rejestrują różne rodzaje produktów spożywczych, a oprogramowanie do interpretacji obrazów sprawdza jakość zgrzewów, etykiet, produktów w plastrach, opakowań. Tajemnica efektywności tkwi w połączeniu kamer i łatwego w obsłudze oprogramowania, tworzonego na przestrzeni niemal 20 lat.
Rozwój produktu sprawia, że technologie są dostępne dla każdego
Dzięki systemowi VisioPointer producenci żywności mogą teraz automatycznie wykrywać zanieczyszczenia obszaru zgrzewu i wady jakościowe, nieprawidłowe etykiety, oznaczenia daty oraz wadliwe opakowania.
- Celem Arla Foods jest wyeliminowanie błędów w produktach końcowych. Chcemy dostarczać produkty na półki sklepowe w idealnym stanie. Przed zakupem systemu TriVision mieliśmy wiele przestojów produkcyjnych. Nowy system zaradził wielu błędom na wszystkich etapach produkcji, a liczba reklamacji klientów znacznie się zmniejszyła. Bardzo zyskaliśmy na tym rozwiązaniu - mówi Bjarne Randrup Nielsen, odpowiedzialny za linię produkcyjną, Arla Foods.
- Zaktualizowana wersja systemu VisioPointer umożliwia wdrożenie tej technologii bez konieczności przebudowy całego zakładu produkcyjnego. Niewielkie rozmiary urządzenia powodują, że pasuje do każdej linii produkcyjnej. Dzięki naszemu inteligentnemu modułowi produkcyjnemu problemy z maszynami wykrywamy już na wczesnym etapie. Stąd też można je rozwiązać zanim doprowadzą do problemów z jakością na masową skalę - mówi Neckelmann.