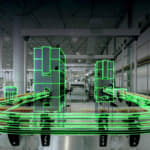
Zrównoważony rozwój ma wysoki priorytet dla współczesnych firm z branży pakowanych towarów konsumpcyjnych (ang. Consumer Packaged Goods - CPG). Kierując się odpowiedzialnością za środowisko, przepisami rządowymi oraz preferencjami klientów, firmy z branży CPG aktywnie poszukują sposobów na dekarbonizację linii pakujących i wykorzystanie ekologicznych materiałów opakowaniowych. Wiele z nich zaczęło monitorować w czasie rzeczywistym zużycie energii swoich maszyn i zmodernizowało krytyczne obszary procesów pakowania, stosując dwie kluczowe technologie: instalacje pneumatyczne i zgrzewanie ultradźwiękowe.
Podczas gdy firmy od dawna polegają na sprawdzonej wydajności pneumatyki w swoich liniach pakujących, najnowsze urządzenia pneumatyczne oferują specjalistyczne możliwości i łączność, które mogą pomóc zoptymalizować zużycie energii, poprawić współczynnik efektywności sprzętu (ang. Overall Equipment Efficiency - OEE) oraz zmaksymalizować produkcję. Jednocześnie zgrzewanie ultradźwiękowe zapewnia większą precyzję, niezawodność i wydajność niż tradycyjne zgrzewanie termiczne, pomagając zminimalizować ilość odpadów, poprawić kompostowalność opakowań i zredukować zużycie energii.
Oto trzy sposoby, dzięki którym firmy z branży CPG mogą wdrożyć te zrównoważone technologie, aby zmniejszyć wpływ na środowisko oraz zwiększyć wskaźnik OEE swoich linii pakujących.
Optymalizacja wykorzystania sprężonego powietrza
Sprężone powietrze jest wykorzystywane do obsługi urządzeń i zasilania procesów w liniach pakujących, w tym do produkcji butelek. Podczas gdy powszechność sprężonego powietrza zwiększa potencjał strat energii, istnieją narzędzia, których można użyć w celu zoptymalizowania jego wykorzystania. Jeszcze nie tak dawno nie było skutecznego sposobu oceny zużycia sprężonego powietrza. Zmieniła to transformacja cyfrowa instalacji pneumatycznych. Współczesne inteligentne urządzenia pneumatyczne zapewniają pełniejszy obraz wydajności systemu pneumatycznego, a także przydatne informacje dla lepszego zrozumienia i skutecznego kontrolowania zużycia energii przez linie pakujące.
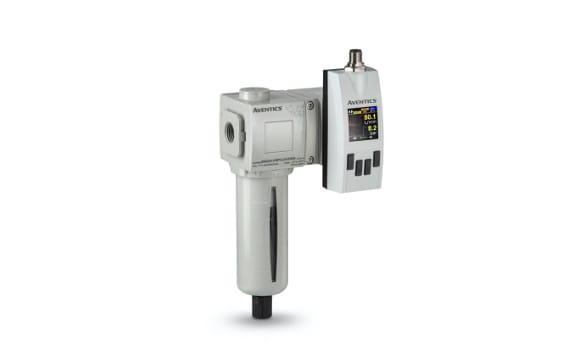
Inteligentne czujniki, połączone z brzegowymi urządzeniami obliczeniowymi, mogą stale monitorować przepływ powietrza w systemie i w czasie rzeczywistym rejestrować przepływ, ciśnienie i prędkość siłownika. Przy odpowiednim zrozumieniu z wykorzystaniem analizy brzegowej dane te mogą pomóc przedsiębiorstwom wykryć powstałe wycieki i zoptymalizować przepływ sprężonego powietrza. Dane te mogą również pomóc operatorom w wyraźniejszym dostrzeżeniu powiązań między ciśnieniem powietrza, jego przepływem oraz prędkością siłownika. Dzięki lepszemu zrozumieniu prawdziwej natury tych powiązań operatorzy mogą określić optymalny punkt, w którym sprężone powietrze jest używane w ich procesach pakowania. Jeśli analizowane ciśnienie wejściowe jest większe niż wymaga tego proces i zużywane jest więcej sprężonego powietrza niż potrzeba, operatorzy mogą zmniejszyć ciśnienie i modulować przepływ powietrza przy zachowaniu tego samego czasu cyklu siłownika. Optymalizując ilość sprężonego powietrza w celu spełnienia wymogów eksploatacyjnych bez wpływu na produkcję, przedsiębiorstwa mogą zminimalizować zużycie energii.
Oprócz optymalizacji zużycia sprężonego powietrza, oprogramowanie monitorujące może również pomóc operatorom wykrywać wycieki niemalże w czasie rzeczywistym. Po wykryciu wycieku system wysyła powiadomienie do działu utrzymania ruchu, który może skontrolować problematyczny sprzęt. Dzięki temu operatorzy mogą znacznie szybciej reagować na wycieki sprężonego powietrza, zapobiegając jego stratom i redukując emisje.
Przedsiębiorstwa, które wdrożyły rozwiązania pneumatyczne do wczesnego wykrywania wycieków i zoptymalizowanego zużycia powietrza, poprawiają wskaźnik OEE i z reguły redukują koszty sprężonego powietrza od 10% do 20% i nawet o 10% ograniczają swój ślad węglowy.