Monitorowanie systemu może też przyczynić się do zredukowania przestojów. Firmy nie muszą już planować przestoju i zlecać technikom badania każdej maszyny pod kątem wycieków, a miejsca wycieków są uszczelniane, zanim spowodują wahania ciśnienia systemu. Wahania wynikające z nieszczelności mogą sprawiać, że maszyny będą wykonywały więcej cykli, niż jest to konieczne.Ta dodatkowa praca przyczynia się do marnowania energii, przedwczesnego zużycia sprzętu i komponentów oraz do zwiększenia nakładów na konserwację.
Perfekcyjna produkcja butelek PET
Pneumatyczne systemy przygotowania zwiększają wydajność i zapewniają lepszą kontrolę powietrza pod niskim i wysokim ciśnieniem, używanego przez siłowniki kształtek wstępnych oraz na etapie rozszerzania butelek w drodze rozdmuchiwania. Kompaktowe, wysokowydajne bloki wydmuchowe zapewniają kontrolę zwiększania objętości butelek za pomocą funkcji przedmuchiwania, wdmuchiwania, recyklingu i wydmuchiwania.
Niektórzy dostawcy jeszcze bardziej zwiększyli wydajność i zrównoważony charakter instalacji pneumatycznych SBM. Na przykład jeden z dostawców oferuje proporcjonalny zawór sterujący opracowany dla etapu rozprężania przed rozdmuchiwaniem w produkcji PET, który zastępuje przepływ pod wysokim ciśnieniem z funkcją wł./wył. i rewolucjonizuje ten etap produkcji butelek. Tam, gdzie dotychczasowy przepływ pod wysokim ciśnieniem z funkcją wł./wył. wyznaczał jednolite natężenie przepływu w procesie rozdmuchu, nowe sterowanie moduluje przepływ w celu dostosowania rozszerzania każdej butelki w formie.
Ta zaawansowana technologia łączy specjalnie zaprojektowany zawór proporcjonalny, elektronikę sterującą i oprogramowanie, które może zapamiętywać wartości zadane sekwencji rozdmuchiwania w zaworze lub reagować na sygnały ze sterownika PLC, który steruje procesem rozdmuchu. Zwiększanie się butelek jest inteligentnie modulowane, dzięki czemu użytkownicy końcowi mogą doskonalić proces rozszerzania się podgrzanej butelki w formie.
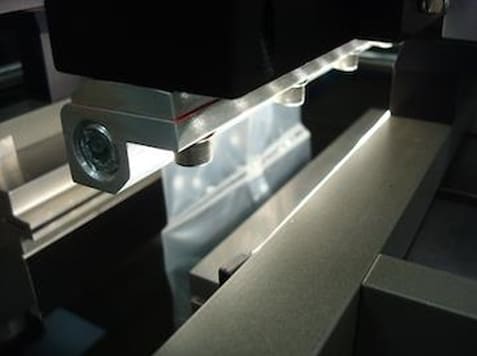
System może też rejestrować informacje dotyczące jakości każdego rozdmuchu, zapewniając producentom butelek krytyczne dane niezbędne do udoskonalania procesu i minimalizowania liczby odrzuconych, zmarnowanych butelek. Dostarcza również dane z monitorowania, które pomagają w planowaniu konserwacji rutynowej i zapobiegawczej.
Technologia proporcjonalna do rozdmuchu butelek PET wynosi pneumatykę na zupełnie nowy poziom zrównoważonego rozwoju dla tego procesu. Przyczynia się do zmniejszenia zużycia materiałów dzięki możliwości dostosowania ścian butelek i formowania kształtu, a także tworzenia cieńszych i lżejszych pojemników. Oszczędza również energię przez potencjalne zmniejszenie ciśnienia rozdmuchu powietrza wymaganego do zapewnienia wysokiej jakości formowania butelek oraz zmniejszenie temperatury podgrzewania w piecu, w którym następuje rozdmuch wstępny.
Oprócz oszczędzania energii, technologia proporcjonalna do rozdmuchiwania PET umożliwia uzyskanie dużej przepustowości produkcji butelek o bardziej złożonych kształtach, co jest ważną kwestią dla celów marketingowych rozlewni. Zwiększa również elastyczność produkcji, ponieważ proces można łatwo regulować za pomocą oprogramowania/sterownika PLC dla każdej stacji rozdmuchu w maszynie i dostosować do dalszych ulepszeń bez konieczności zatrzymywania produkcji.
Wdrożenie zgrzewania ultradźwiękowego
Aby zwiększyć ekologiczność procesu zgrzewania, zgrzewanie ultradźwiękowe oferuje wiele korzyści w porównaniu z tradycyjnym zgrzewaniem termicznym. Jest precyzyjne, niezawodne i wydajne, co pozwala użytkownikom zmniejszyć zużycie energii, zminimalizować marnowanie produktów i opakowań oraz zwiększyć możliwości recyklingu i kompostowalność opakowań. Można je również stosować do łączenia materiałów biodegradowalnych. Ta zrównoważona technologia może ostatecznie obniżyć zużycie energii nawet o 25% i zmniejszyć emisję dwutlenku węgla nawet o 75%.
Systemy zgrzewania ultradźwiękowego zużywają po prostu mniej energii niż systemy zgrzewania kondukcyjnego. Procesy zgrzewania ultradźwiękowego zużywają energię w krótkich seriach, a nie w sposób ciągły, jak ma to miejsce w procesach zgrzewania kondukcyjnego. Na przykład, aby wykonać 100 zgrzewów na minutę w ciągu dwóch ośmiogodzinnych zmian dziennie, typowy system zgrzewania kondukcyjnego potrzebuje czterech 500-watowych grzałek kasetowych (2000 W na godzinę lub 32 000 W na dzień), aby stale utrzymywać temperaturę roboczą. Z drugiej strony, zgrzewarka ultradźwiękowa wykonująca te same operacje, byłaby wyposażona w zasilacz o mocy zaledwie 1500 W i byłaby zasilana tylko w krótkich seriach (np. ~200 ms na zgrzew), zużywając energię przez zaledwie 20 sekund w każdej minucie produkcji.