
Roboty współpracujące lub inaczej coboty (z ang. collaborative robots, cobots) stwarzają dodatkowe możliwości automatyzacji w przemyśle tworzyw sztucznych. Charakteryzuje je m.in. możliwość pracy w małej przestrzeni roboczej, ramię w ramię z człowiekiem, szybkość wdrożenia i przezbrajania do nowych zadań oraz intuicyjne programowanie i obsługa. Mogą wspierać m.in. takie procesy jak formowanie wtryskowe, obsługa maszyn czy pakowanie i paletyzację, zarówno w dużych przedsiębiorstwach, jak i kilkuosobowych zakładach.
Producenci na całym świecie inwestują w automatyzację. Badanie "Barometr robotyzacji MŚP" przeprowadzone w Polsce pod koniec 2019 roku i obejmujące także firmy z sektora przetwórstwa tworzyw sztucznych pokazało, że najistotniejszym czynnikiem motywującym MŚP do robotyzacji jest poprawa efektywności produkcji (82,7%). Następnie firmy wymieniały: zwiększenie wolumenu wytwarzanych produktów (71,2%), skrócenie czasu od zamówienia do realizacji (68,3%), wyeliminowanie błędów ludzkich (61,5%), trudności z zatrudnieniem lub utrzymaniem personelu (60,6%), podniesienie konkurencyjności (58,7%) oraz bezpieczeństwa pracy (53,8%) a także standaryzację procesów (53,8%).
Wykorzystanie robotów współpracujących pozwala zmniejszyć kontakt pracowników ze szkodliwymi gazami, pyłami i opiłkami powstałymi podczas produkcji tworzyw sztucznych i polimerów. Coboty mogą także przenosić ostre lub gorące elementy. Możliwość pracy przez całą dobę oraz powtarzalność ruchu na poziomie 0,03 mm (w przypadku cobotów Universal Robots) pozwalają maksymalnie wykorzystać moce produkcyjne przy zachowaniu spójnych standardów jakości. Lekka konstrukcja i niewielkie gabaryty pozwalają cobotom pracować także w zakładach o bardzo ograniczonej przestrzeni roboczej.
Zastosowania i możliwości
Coboty umożliwiają niemal całkowitą automatyzację procesów formowania wtryskowego. Gwarantują stałą jakość, precyzję, a także jednolity poziom dozowania nawet po wielu powtórzeniach. Ponadto zwiększają precyzję poszczególnych podprocesów i przyczyniają się do ograniczenia ilości powstających odpadów. Roboty współpracujące dobrze sprawdzają się także w obsłudze maszyn, między innymi obrabiarek CNC, wtryskarek, pras krawędziowych czy pras tłoczących. Ich wdrożenie pozytywnie wpływa na tempo i jakość, przy jednoczesnym ograniczeniu ryzyka urazów związanych z pracą przy ciężkich maszynach. Możliwość zamontowania różnych elementów wykonawczych i systemów przetwarzania obrazu sprawia, że w zależności od potrzeb firma może wykorzystać cobota do pracy przy różnych etapach produkcji, np. umieszczaniu elementów we frezarce czy paletyzowaniu obrobione części. Bardzo ważną fazą produkcji jest także wykańczanie powierzchni - coboty mogą pracować z różnego rodzaju tworzywami, zachowując odpowiednie parametry i zapewniając wysoką, spójną jakość finalnego produktu.
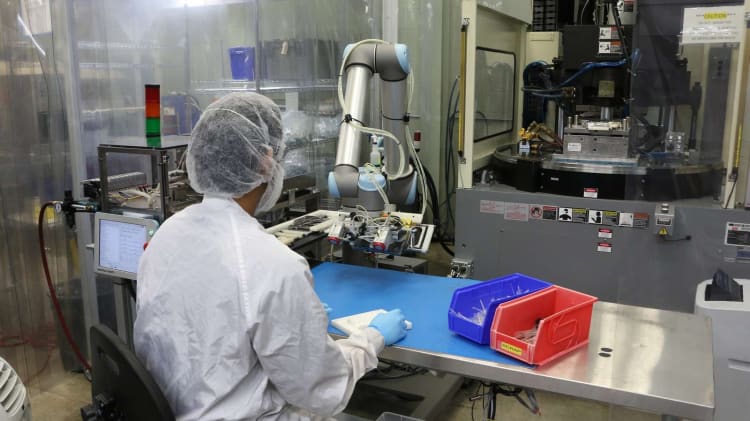
Coboty - zastosowania, przykłady z rynku
2K Trends, czeski producent elementów z tworzyw sztucznych produkowanych na potrzeby koncernów samochodowych wdrożył cobota UR10, który realizuje pełen cykl produkcyjny, zapewniając optymalizację pracy i rozwiązując jednocześnie problem braków kadrowych. UR10 umieszcza materiał wyjściowy – na ogół w postaci granulek – w formie i w ten sposób rozpoczyna proces formowania wtryskowego. Zakończeniem tego procesu jest wyjęcie przez cobota gotowych kształtek z formy i umieszczenie ich na taśmie przenośnika. Jest to zajęcie monotonne, a jednocześnie wymagające niezwykłej precyzji – doskonale nadające się do zrobotyzowania. Obecnie cobot UR10 niemalże samodzielnie obsługuje maszynę, dzięki czemu firma nie musi angażować w ten proces pracowników. Dodatkowo zaletą ramienia UR10 jest duży zasięg, który pozwala na efektywne obsługiwanie całej wtryskarki.
Firma Dynamic Group zainstalowała trzy roboty UR10 przy formowaniu wtryskowym i kompletowaniu zestawów. Pierwszy robot zwykle obsługuje pełny cykl maszyny, czyli podnosi i wstawia na swoje miejsca "ramki formierskie" utrzymujące elementy, które mają być formowane na wtryskarce, transportuje elementy do przycinarki, umieszcza część przed operatorem w celu dalszej obróbki, po czym naciska przycisk, aby ponownie aktywować cykl. W drugim zastosowaniu korzysta się z tradycyjnego kartezjańskiego robota, który upuszcza uformowany element na prowadnicę ślizgową, skąd podnosi go robot UR i umieszcza go w uchwycie oddzielającym, po czym stawia część na stole przed operatorem w celu przeprowadzenia kontroli jakości. Trzeci robot służy do rozmieszczania elementów.
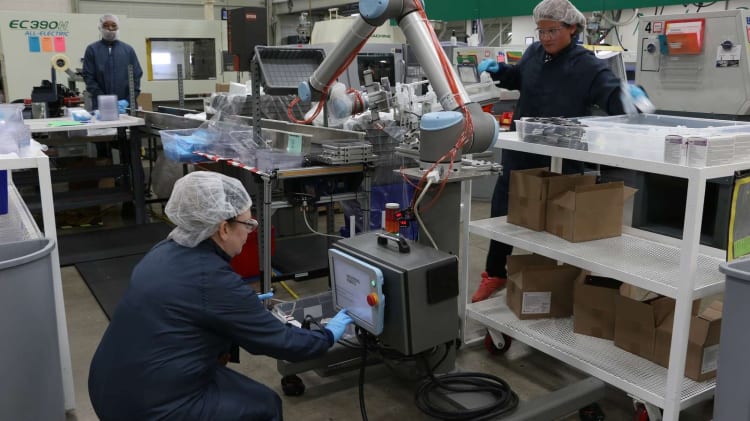
- W porównaniu do tradycyjnych robotów, powiedziałbym, że roboty UR o wiele łatwiej się uczą i łatwiej je programować przy użyciu aplikacji typu "przeciągnij i upuść". Można również zaprogramować robota w trybie "teach mode", gdzie po prostu chwyta się ramię robota i przesuwa je w wybrane miejsce, ucząc w ten sposób robota, gdzie ma się znaleźć. Po zakończeniu konfiguracji punktów po prostu naciska się przycisk play, a robot będzie odtwarzał te ruchy - mówi Joe McGillivray, CEO Dynamic Group.
Liczne studia przypadku opisujące wdrożenia cobotów dobrze ilustrują wszechstronność tych rozwiązań. Dzięki łatwości programowania i obsługi są one narzędziem, które w rękach operatora otwartego na technologię może pomóc firmom szybciej rozwijać się i skuteczniej konkurować na rynku. Więcej informacji na temat zastosowania cobotów w przemyśle tworzyw sztucznych można uzyskać na stronie: https://www.universal-robots.com/pl/industry/
Źródło: Universal Robots