Jakie kwestie należałoby rozważyć, dokonując oceny projektu systemu gorących kanałów w krytyczny, ale konstruktywny sposób?
Tak naprawdę wszystko jest ważne. Jak już nadmieniłem, idealnym przypadkiem jest współpraca trzech stron, czyli przetwórcy, narzędziowni i dostawcy układu gorącokanałowego. W tym przypadku należy rozpatrywać układ g/k po pierwsze jako rozwiązanie konkretnego problemu technicznego, a po drugie jako rozwiązanie pod kątem komercyjnym, pozwalające zmaksymalizować moce produkcyjne i zminimalizować straty.
Niestety, często bywa, że oczekiwania od układu g/k przez narzędziownię nie są zbieżne z wymogami przetwórcy, a bywa i tak, że są totalnie przeciwne. Aby pogodzić oczekiwania obu stron, niezbędna jest współpraca – i to już na etapie powstawania konstrukcji samego wyrobu. Udział dostawcy na tak wczesnym etapie gwarantuje optymalny dobór rozwiązania dla obydwu stron. Argumenty, które dla przetwórcy są kluczowe (np. redukcja zużycia energii) nie są żadnym argumentem dla narzędziowni i na odwrót – to, że dysza ma zbyt dużą średnicę i nie pasuje do konstrukcji formy, nie stanowi kryterium wyboru układu dla przetwórcy, a jest kluczowym argumentem dla narzędziowni.
W związku z tym, to dostawca układu g/k ma obowiązek stworzenia listy priorytetów i pogodzenia oczekiwań od grzanego kanału. I tak, przetwórca powinien określić roczny wolumen produkcyjny, poinformować o rodzaju przetwarzanego tworzywa, ew. jaki jest poziom dopuszczalnego dodatku w postaci recyklatu. Powinien też zdefiniować oczekiwania co do czasu cyklu, częstotliwości zmiany koloru, ale przede wszystkim przekazać swoje doświadczenie (te złe i te dobre) z podobnymi aplikacjami. Jak wielokrotnie wspominałem, sam dobór dostawcy powinien być przede wszystkim podyktowany aspektami ekonomicznymi, ale uwzględniającymi całkowity koszt użytkowania, a nie wyłącznie ceną zakupu układu g/k. Niezbędną stroną jest oczywiście narzędziownia, która powinna zdefiniować wszelkie aspekty techniczno-konstrukcyjne.
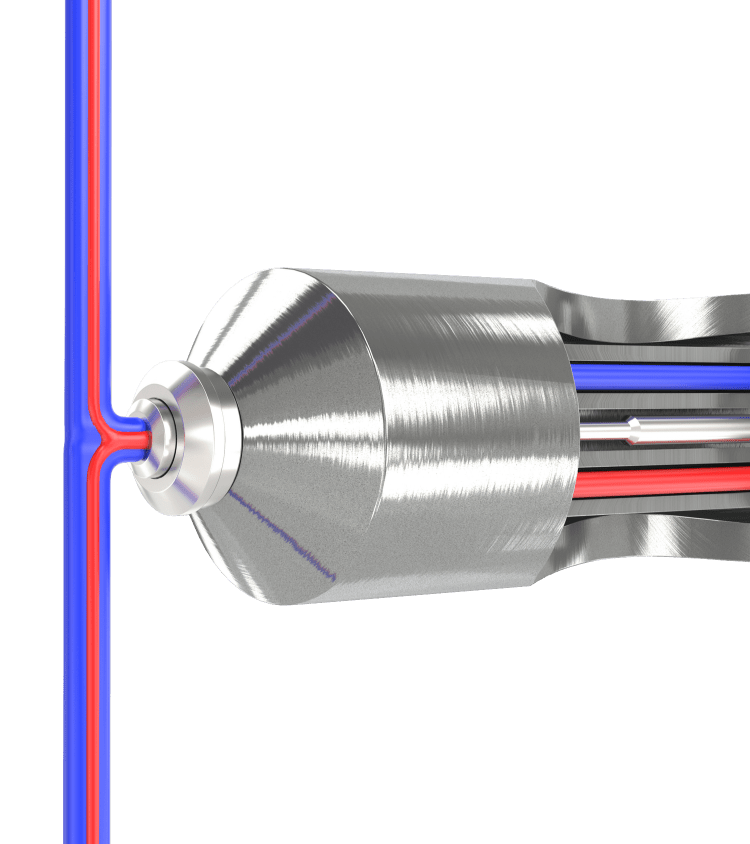
Dysza Mold-Masters do technologii współwtrysku (ang.co-injection)
Obecnie jednym z najczęściej poruszanych problemów jest kwestia zamkniętego obiegu surowców i ogólnie próby rozwiązania problemu odpadów. Z jednej strony niezwykle popularne stały się regranulaty, z drugiej szukamy alternatyw dla standardowych polimerów; myślę tu o tzw. biotworzywach. Jaka jest rola układów g/k w przetwórstwie tych materiałów?
Tworzywa sztuczne stały się wrogiem publicznym nr 1. I nic dziwnego. Według Surfers Against Sewage, w 1950 r. 2,5 mld ludności świata wyprodukowało 1,5 mln ton plastiku; w 2016 r. globalna populacja licząca ponad 7 mld ludzi wyprodukowała ponad 320 mln ton plastiku. Do 2034 r. liczba ta ma się podwoić.
Nie można jednak demonizować wszystkiego, co jest wykonane z tworzywa sztucznego. Wydaje się, iż największym dziś problemem są ograniczone moce utylizacji czy recyklingu. Czas też pokaże, czy właśnie wprowadzona dyrektywa SUP pozwoli ograniczyć obrót produktów jednorazowego użytku z tworzyw sztucznych oraz produktów wykonanych z oksydegradowalnych tworzyw sztucznych. Dostawcy układów g/k nie pozostają bierni na stawiane wyzwania i już dość dawno wprowadzili do swojej oferty rozwiązania pozwalające przetwarzać tworzywa biodegradowalne, takie jak np. PLA, PHA, PHB, czy też tworzywa kompostowalne. Oczywiście wymogi stawiane takim układom są ekstremalnie wysokie. Tworzywa bio charakteryzują się bardzo wąskimi oknami przetwórczymi z uwagi na wrażliwość na temperaturę oraz ścinanie. Dodatkowo, jeśli konstrukcja układu g/k nie będzie zoptymalizowana pod kątem takich właśnie tworzyw, same w sobie będą generowały dodatkowe problemy lub będą nasilały już istniejące.
Firma Mold-Masters poświęciła wiele czasu na testowanie praktycznie wszystkich obecnie dostępnych na rynku tworzyw z grupy bio. We współpracy z University of Massachusetts oraz czołowymi dostawcami tworzyw stworzono matrycę, która pozwala na dobór układu g/k w najbardziej optymalny sposób w zależności od zastosowanego tworzywa. Oprócz typowych aplikacji, tworzywa bio coraz częściej stosowane są do bardziej skomplikowanych procesów, np. procesu współwtrysku (ang. co-injection). Tu również najbardziej zaawansowane rozwiązania posiada Mold-Masters, który wykorzystuje dysze umożliwiające połączenie dwóch różnych tworzyw w jedną trójwarstwową strukturę. Dzięki zastosowaniu wysokowydajnej bariery jako warstwy rdzeniowej opakowań do żywności, współwtrysk wydłuża okres jej przydatności do spożycia, pozwalając zachować świeżość i smak do 5 razy dłużej niż w przypadku struktury jednowarstwowej.
Z perspektywy przetwarzania współwtrysk zwiększa produktywność, eliminując potrzebę procesów wtórnych i minimalizując ilość odpadów. Według firmy Mold-Masters może to również zredukować użycie drogich materiałów barierowych, które mogą stanowić zaledwie 2% masy wypraski. Współwtrysk tworzyw bio jest często wykorzystywany w przypadku aplikacji opakowaniowych. Jednym z przykładów jest wytwarzanie jednorazowych kapsułek do kawy. Warstwą wewnętrzną może też być recyklat, dzięki czemu produkcja niektórych detali może stać się bardziej ekonomiczna z uwagi na zmniejszenie zapotrzebowania na tworzywo pierwotne.
Jak pana zdaniem będą kształtować się tendencje rozwojowe w technologii układów g/k?
Jestem przekonany, że technologia układów gorącokanałowych będzie nadal szybko się rozwijała i coraz bardziej ewaluowała w kierunku digitalizacji i automatyzacji. Już dziś układ g/k komunikuje się z pozostałymi elementami nie tylko gniazda produkcyjnego, ale i całego zakładu produkcyjnego, wymieniając między sobą dane. Punktem wyjścia dla rozwoju nowoczesnego wytwarzania jest przemysłowy internet rzeczy (ang. IoT). Jest to dynamiczna sieć złożona z fizycznych obiektów wyposażonych w sensory, autonomicznych czujników, platform i aplikacji zdolnych do zbierania danych oraz dzielenia się nimi między sobą i otoczeniem.
Kto wie, być może w przyszłości układy g/k zasilane będą dedykowanymi panelami fotowoltaicznymi lub ogniwami perowskitowymi? Analizując okresy przejść między kolejnymi etapami industrializacji, nie sposób nie stwierdzić przyspieszenia. Spoglądając wstecz: pomiędzy erą Przemysłu 2.0 a 3.0 upłynęło stulecie, ale już przejście od Przemysłu 3.0 do 4.0 zajęło niecałe pół wieku. Jeśli uznamy, że rok 2011 uważany jest za początek ery przemysłu 4.0, a postęp będzie przyspieszał tak, jak dzieje się to do tej pory, to możemy założyć, że około roku 2030 wejdziemy w erę Przemysłu 5.0. Sam jest ciekaw, czym nas on zaskoczy…
Rozmawiał: Jacek Leszczyński