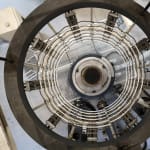
Folie polietylenowe produkowane metodą rozdmuchu mają bardzo szerokie zastosowanie w przemyśle jako materiały opakowaniowe. Zazwyczaj są elementem większego systemu pakowania, znakowania i zabezpieczania gotowych wyrobów
W większości przypadków folie są surowcem/półproduktem, który wymaga dalszej obróbki (drukowanie, laminowanie, zgrzewanie…) albo stanowią część automatycznego lub półautomatycznego procesu pakowania. Procesy takie należą do bardzo wrażliwych, co z kolei stawia wymagania jakościowe na bardzo wysokim poziomie. Wszelkie defekty, nierówności nawoju, zmarszczki, brak prostoliniowości, zbyt duże rozrzuty grubości folii powodują spowolnienie linii, przestoje, zwiększają odpad lub kompletnie uniemożliwiają dalszą pracę.
Istnieją trzy podstawowe grupy czynników będących powodem problemów i wad produkcyjnych: mechaniczne, materiałowe i ludzkie. Żeby w odpowiedni sposób zdiagnozować problem, należy znać zależności przyczynowo-skutkowe pomiędzy czynnikami mającymi wpływ na proces produkcyjny. Wymaga to dużej wiedzy i cierpliwości w diagnozowaniu podstaw problemu. Może się zdarzyć, że na problem jakościowy folii ma wpływ kilka nakładających się składowych, a wyeliminowanie jednej z nich nie likwiduje go w 100%. Dlatego bardzo istotne jest metodyczne podejście do problemu i dogłębna analiza procesu. W dalszej części artykułu rozpatrzymy przykładowe problemy mechaniczne (maszynowe).
Niezależnie od tego, czy dysponujemy linią technologiczną jedno- czy wielowarstwową, każda z nich składać się będzie z tych samych, podstawowych podzespołów. Są to napęd, układ plastyfikujący, głowica, układ chłodzenia, odciąg górny, układ nawijania, sterowanie. Oczywiście każda z linii może być wyposażana w dodatkowe układy kontroli, pomiaru, prowadzenia wstęgi, drukarki, aktywatory itd.
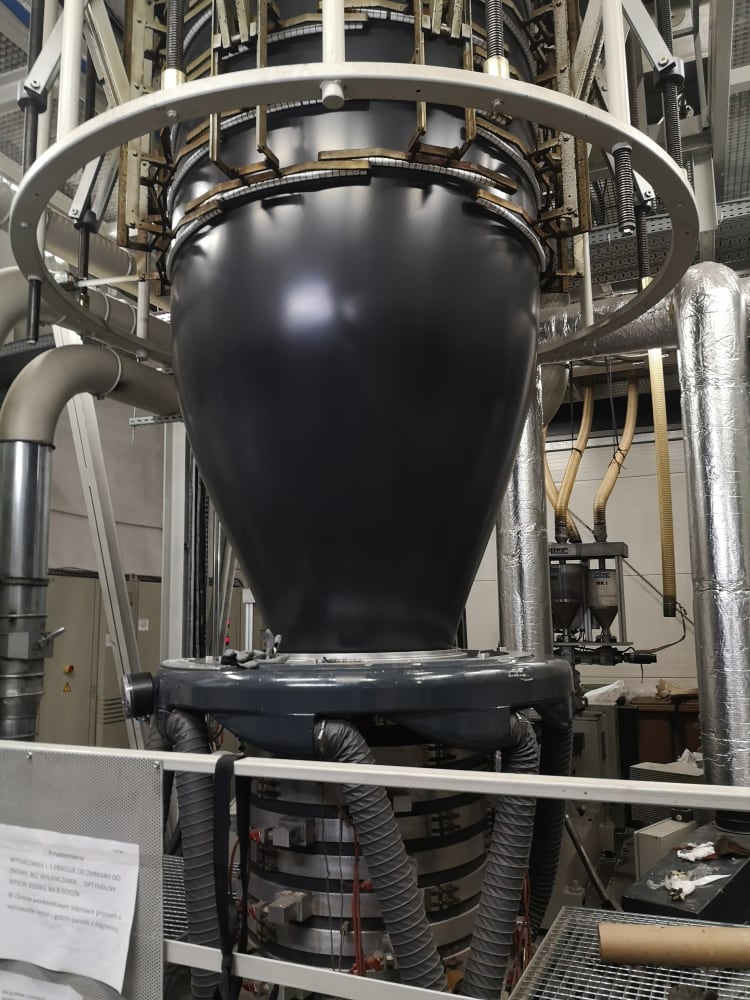
Układ plastyfikujący
Zużywanie się układu plastyfikującego jest jedną z podstawowych bolączek każdego wytwórcy folii. Jeżeli w produkcji używane są materiały pochodzące z recyklingu czy wypełniacze mineralne, degradacja układu następuje odpowiednio szybciej niż przy stosowaniu materiałów pierwotnych.
Problem ze zużywaniem układu polega głównie na tym, że trzeba płynnie reagować na postępujące zmiennie warunki pracy. Wydajność układu spada z każdą przerobioną toną surowca. Nie jest to proces, który można zauważyć ''gołym okiem'', ale porównując parametry pracy w przekroju np. miesiąca można zauważyć, że często te same produkcje trzeba wykonywać na innych ustawieniach. Dopóki sterowanie na to pozwala, nie rzutuje to na wydajność linii. Wymaga jedynie od operatorów korygowania parametrów maszyny w celu uzyskania odpowiedniego wyrobu. Poważny problem pojawia się w momencie, gdy zużycie układu przekroczy pewną graniczną wartość i tworzywo jest podawane w sposób nierównomierny do głowicy. Można to w łatwy sposób zauważyć na wskaźniku ciśnienia znajdującego się na końcu układu plastyfikującego lub na skokach obciążenia napędu.