Układ chłodzenia
Do jednego z bardziej zaniedbywanych elementów należy układ chłodzenia folii. Nie ma znaczenia, czy jest to prosty układ z wentylatorem nadmuchowym i pierścieniem z jednym wylotem powierza, czy zaawansowany system chłodzenia wewnętrznego (IBC) i skomplikowany pierścień chłodzący. Wszystkie te elementy zużywają się w czasie pracy, powodując problemy z produkcją. W przypadku stosowania IBC uzyskanie folii odpowiedniej jakości może utrudniać ''parafina'' odkładająca się w pierścieniu chłodzącym w rurach i wentylatorze odprowadzającym powietrze. Zaburzenia przepływu powietrza w takich wypadkach mogą być kompensowane siłą nadmuchu, ale i to wystarcza tylko do pewnego czasu.
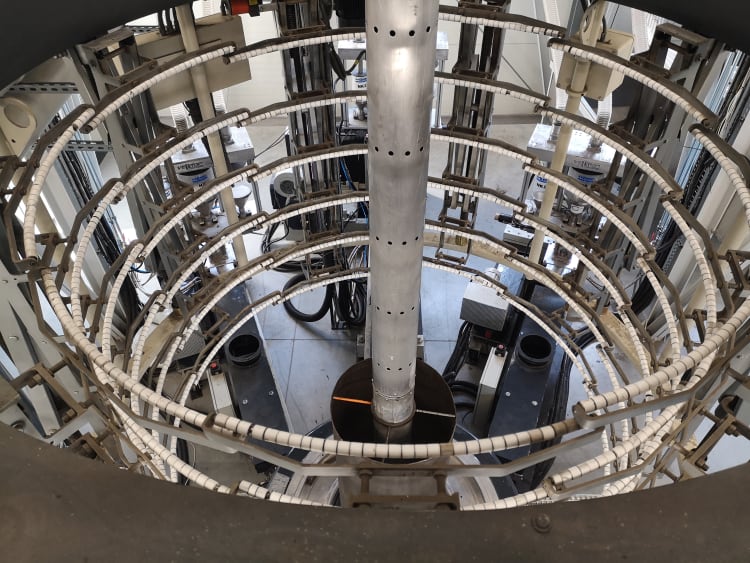
Rezultatem jest zawsze spadek wydajności linii produkcyjnej. Operatorzy są zmuszeni do spowolnienia maszyny, tłumacząc to brakiem możliwości wychłodzenia folii. Zazwyczaj przyczyn szuka się w błędach elektroniki i sterowania. Zachowanie balona w trakcie produkcji wskazuje na problemy z działaniem czujników odpowiedzialnych za kontrolę jego średnicy. Czasami wystarczy proste czyszczenie elementów chłodzenia bądź wymiana rur, zamiast kosztownej ingerencji w sterowanie.
Innym częstym problemem są przedmuchy na pierścieniu chłodzącym wynikające z nieszczelności. Może się to zdarzyć przy długiej eksploatacji pierścienia bez wymiany uszczelnień. W tym wypadku może dojść do zmniejszenia intensywności chłodzenia na jakimś fragmencie balona. Oczywiście pierścienie z bocznymi dolotami powietrza powinny zapobiegać takim zdarzeniom, ale często taka nieszczelność wiąże się z tym, że pierścień nie był konserwowany przez długi okres i ma miejscowo ''zarośnięty'' lub zapchany wylot powietrza, a taki układ jest przyczyną wielu wad produkcyjnych.
Odciągi
Odciąg górny folii to istotny element linii produkcyjnej, mający duży i bezpośredni wpływ na jakość gotowego wyrobu. Jego zadaniem jest odebranie uformowanego tworzywa z zadaną prędkością. Parametrem tym regulujemy grubość wstęgi folii. Podstawowymi częściami odciągu są wałki - gumowy i metalowy lub dwa gumowe (w zależności od linii). Z tego względu że znajdują się one na wysokości kliku lub kilkunastu metrów, w zależności od rodzaju maszyny zdarza się, że są brudne i otłuszczone z powodu odkładającej się parafiny, pyłów i kurzu. Z biegiem czasu taka mieszanka twardnieje, powodując nierówny docisk wałków, co skutkuje pojawieniem się defektów folii. Podobny skutek może wywołać brak regularnych przeglądów i wymiany łożysk na wałkach. Przepracowanie lub uszkodzone łożysko powoduje opadnięcie wałka lub jego blokowanie się w czasie pracy.
Nie można zapominać, że wałki gumowe są elementem eksploatacyjnym i tak samo jak łożyska należy je wymieniać lub regenerować, jeśli tylko jest taka możliwość. Guma w czasie pracy ugniata się i twardnieje. Dodatkowym czynnikiem przyspieszającym ten proces jest temperatura, która zazwyczaj jest wyższa niż dopuszczalna. Brak elastyczności gumy może spowodować uciekanie powietrza ze środka balona, głównie przy produkcji folii z zakładkami, co przy systemach z kontrolą wielkości balona wymusza ciągłą regulację ilością podawanego powietrza, a w układach bez kontroli powoduje przewężenia na szerokość wstęgi.
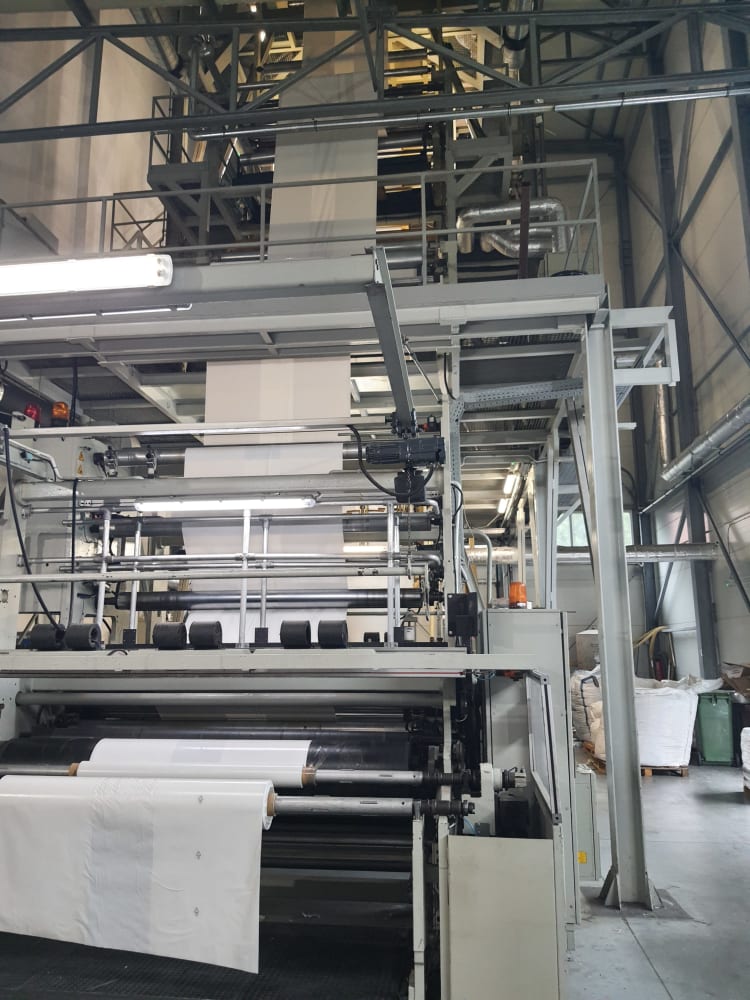
Równie istotnym elementem jest bieżąca kontrola i czyszczenie wałków prowadzących wstęgę folii do nawijarki. Tak jak w przypadku wałków odciągu, każde uszkodzone łożysko może prowadzić do przeciągnięć lub nierównych nawojów folii.
Ostatnim elementem linii produkcyjnej zazwyczaj jest nawijarka (odciąg dolny). W tym wypadku dbałość o jakość prowadzenia wstęgi jest nawet jeszcze ważniejsza. Na nawijaku wciąż można skorygować ewentualne nierówności, fałdki czy zmarszczenia, ale konieczne jest posiadanie idealnego stanu rolek (łożyskowanie, czystość, poziomowanie…).
Do uzyskania prawidłowego nawoju niezbędne jest odpowiednie ułożenie wałka bananowego lub sznurkowego, jeżeli występują takowe w maszynie. Operatorzy linii mają w zwyczaju pomijać niektóre wałki nawijarki; często zdarza się tak z powodu utrudnionego dostępu lub niechęci do ''gimnastykowania się'' przy przeciąganiu wstęgi folii. Ma to miejsce w przypadku linii mniej zaawansowanych technicznie, które nie posiadają kontroli naciągu. Może to skutkować pomarszczoną i pozaginaną folią na gotowej rolce. Naciąg folii powinien być ustawiany i korygowany w zależności od grubości folii i wielkości balona.
W liniach o większych gabarytach nawijarka jest osobnym urządzeniem, które musi zostać idealnie ułożone w stosunku do głowicy i górnego odciągu folii. Poprawność takiego ułożenia należy okresowo kontrolować i w miarę potrzeb korygować; szczególnie na halach, gdzie pracują wózki widłowe.
Poza opisanymi przypadkami istnieje szereg zaniedbań i błędów wpływających na jakość końcowych wyrobów. Najważniejsze przy diagnozowaniu powodów wad produkcyjnych jest metodyczne podejście do sprawy, dogłębna analiza i niewyciąganie pochopnych wniosków. Na prawidłowość procesu produkcji folii wpływa wiele czynników i trzeba je wszystkie brać pod uwagę, dlatego też wymaga on sporego zaangażowania.
Tomasz Gliński
Zdjęcia dzięki uprzejmości firmy Total-Chem Sp. z o.o.