Efektem takiego stanu rzeczy jest pulsacyjne podawanie tworzywa do głowicy, co z kolei powoduje przegrubienia folii występujące co jakiś czas na całej szerokości w kierunku wytłaczania. Dodatkowo skokowy wzrost ciśnienia przed wymiennikiem sit powoduje przedostanie się zanieczyszczeń znajdujących się na sicie, które albo trafią do tworzywa i pojawią się na balonie, albo (co gorsze) zostaną w ustniku głowicy powodując mniejsze lub większe miejscowe przecienienia bądź rysy na folii.
Jeżeli mowa o układzie plastyfikującym, to warto zauważyć że jest on częścią-sercem wytłaczarki. Nawet jeżeli znajduje się w idealnym stanie, nie możemy zapominać o odpowiednim ustawieniu temperatur na maszynie, adekwatnym doborze filtracji na wymienniku sit, czy chłodzeniu na zasypie linii w przypadku układów z rowkowaną strefą zasypu. To wszystko wpływa w sposób pośredni lub bezpośredni na jakość produkowanej folii.
Elementem wytłaczarki jest również napęd, w którego skład wchodzą silniki, przekładnie, koła pasowe, sprzęgła. Dbałość o stan tych poszczególnych części jest bardzo istotna. Dzięki regularnym przeglądom i konserwacji możemy uniknąć problemów z nierównomiernymi obrotami silnika czy uślizgiem pasów klinowych, co w efekcie przekłada się na równość podawania tworzywa i na jakość gotowej folii.
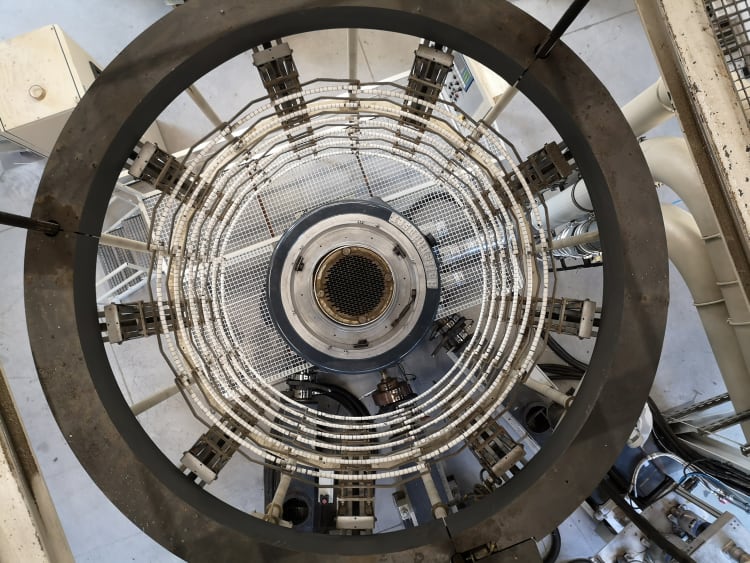
Głowice
Kolejnym elementem linii technologicznej do wytwarzania folii są głowice. Różnią się od siebie w zależności od technologii produkcji (jedno-/wielowarstwowa). Mogą występować w układzie obrotowym lub stacjonarnym. Jest jednak szereg zabiegów (często pomijanych, szczególnie przy produkcji prowadzonej w ruchu ciągłym) dających wymierny efekt jakościowy gotowych wyrobów.
Centrowanie szczeliny - zdecydowanie należy zwrócić uwagę na to, że raz ustawiona przez producenta maszyny, serwis czy operatora szczelina nie zwalnia z obowiązku okresowej kontroli. Głowica jest elementem narażonym na duże i zmienne obciążenia, dlatego tak istotne są przeglądy jej stanu. Często można spotkać gotowe wyroby lub półprodukty foliowe, które nawinięte na rolkę są z jednej strony ''twarde'', a z drugiej ''miękkie''; powodem tego są różnice w grubości folii po obwodzie balona. Można ten efekt zniwelować, stosując głowice lub odciągi obrotowe. Ale to tylko maskuje problem nie rozwiązując go; rozrzuty grubości na folii bowiem nie znikają, są tylko równo rozłożone na rolce.
Czyszczenie ustnika - w trakcie produkcji wokół ustnika powoli odkłada się tworzywo, zarówno z jednej, jak i z drugiej strony. Przez ciągły kontakt z temperaturą głowicy tworzywo to zaczyna się spiekać. Jeżeli pozostawimy taki spiek na odpowiednio długi czas, ''rozrośnie'' się on od do takiego rozmiaru, że zacznie ocierać się o balon. Dodatkowo przy zmianie rozmiaru balona może powodować miejscowe defekty i/lub rysy na powierzchni folii.
Poza czyszczeniem powierzchni ustnika należy dbać o czystość i brak spieków wewnątrz szczeliny. Trzeba co jakiś czas zdemontować wewnętrzny pierścień głowicy i gruntownie wyczyścić, ''zabielić'' jego powierzchnię. W trakcie procesu produkcji folii stosuje się wiele różnych dodatków i modyfikatorów. Zazwyczaj mają one różne temperatury przetwarzania i tendencję do odkładania się i spiekania na powierzchni szczeliny, co prowadzi do wad produkcyjnych na powierzchni folii. Dbałość o idealny stan i czystość ustnika oraz szczeliny jest jednym z kluczowych elementów dla jakości produkowanej folii, niestety bardzo często z powodu czasochłonności tego zabiegu jest on pomijany. Można co prawda stosować środki czyszczące w postaci dodatków lub próbować zapobiegać odkładaniu się tworzywa na metalowych elementach układu przez wykorzystanie dodatków procesowych, ale i to zazwyczaj jest niewystarczające i konieczne jest czyszczenie manualne.
Bardzo istotną kwestią jest ustawienie głowicy. Zachowanie poziomu oraz centralnego ustawienia w stosunku do górnego odciągu bezpośrednio wpływa na jakość produkowanej folii. Tak samo jak w przypadku centrowania, powinno się dokonywać okresowego sprawdzania tych parametrów.